Source: Fraunhofer IPA/Graph: Andrine Theiss
Mobile robotics as the key to matrix production
For matrix production to function optimally, a whole fleet of mobile robots is needed. Ants serve as a role model for orchestrating this dynamic interaction as efficiently as possible. Agha Ali Haider Qizilbash from the Robot and Assistive Systems department gives an insight into his research work.
Published on 09-03-2023
Reading time approx. 8 minutes
An anthill is teeming with creepy-crawlies that, at first glance, seem to be wildly and uncontrollably attempting to find the shortest possible route from A to B as quickly as possible. And yet it is much less random that one might initially think. A similar picture could emerge in terms of future solutions with matrix production: Numerous mobile robots move around a factory floor to enable a seamless production process at the individual stations. The robots may replace the assembly line or assist skilled workers to ensure that the right component or tool is in the right place at the right time. However, the optimal planning of robot deployment remains a challenge. To address these, new software solutions are being developed in the research project “SE.MA.KI”. They mainly address autonomous mobile robots (AMR) and also automated guided vehicles (AGVs) equipped with sensors.
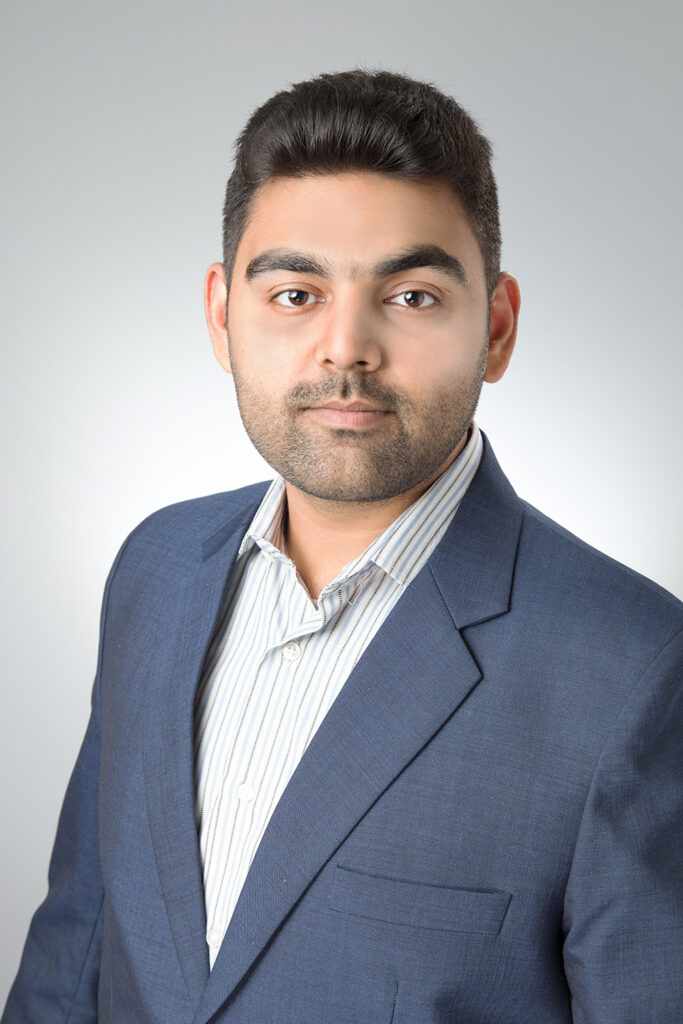
Optimized traffic
The key to successful AMR use for matrix production is optimal planning. Which robot travels along which route to what destination and when? This complex challenge cannot be mastered manually. One existing solution is traffic optimization, which can be implemented using fleet management systems. The aim is to reduce the number of robots moving in a corridor. So, if several robots find themselves in the same corridor, they have to wait and queue. Route markings could also be installed for AGVs in certain locations. These clearly defined routes make it easier to separate the workspace between the vehicle and the person. That kind of solution may well be scalable, but it is also inefficient, because it restricts people’s freedom of movement and other mobile units in production, e.g. forklifts, may also be used less flexibly.
Open planning
The open planning of mobile robots is the better solution to achieve flexible and robust production, as several robots can operate on the factory floor. Each one can avoid collisions with others and still find their way to the destination. Open planning also allows people to move around in the factory for monitoring and work purposes. It also ensures that no robot becomes too important and blocks the route for others or, even worse, creates demarcated zones for specific activities. This adaptability was also one of the ideas that brought matrix production to life to adapt processes and the workshop itself to changes.
Group-based production planning
The approach of group-based production planning is also common to manage and shorten production lead times, and the tasks are collected and grouped in the process. The groups are treated as scheduling units and subgroups as scheduling objects. The approach has proven successful in shortening production lead times compared to traditional approaches. It is therefore logical to use group-based scheduling when managing the distribution of articles to different stations. The merging of material supply, the delivery and distribution of articles in a production environment within a joint perspective can not only reduce the overload of mobile robots, but is also adaptable to the changing requirements of dynamic productions. As the article distributions are programmed for a specific period or batch, fresh requirements that arise at a certain time within the next batch can be taken into account before the orders are centrally processed and scheduled.
These article distributions are classified as orders for processing and must necessarily have an initial position and a delivery destination. By combining orders that have accumulated up to a certain time interval or by using a predetermined list of orders, an order quantity is created that must be processed in the next round. Based on this information and the current locations of all mobile robots in the area, the orders can be processed centrally and assigned to the corresponding orders in sequence. This also optimizes the total distance covered by all robots.
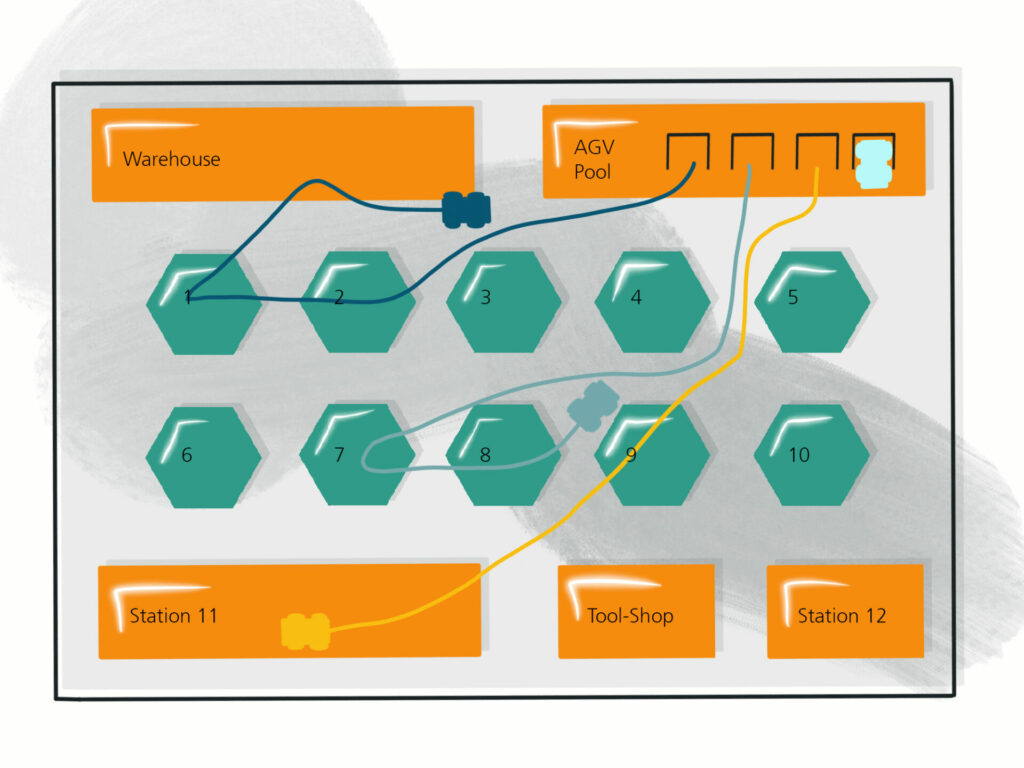
A new bio-inspired approach
However, the approaches presented do not yet solve the deployment planning of mobile robots in an optimal way. On the industry side, the crucial question is: how can a transport task be completed as quickly as possible? And how can the distance covered by the fleet also be as short as possible? This topic is therefore the focus of numerous research activities. Bio-inspired algorithms have been increasingly used. Algorithms based on particle swarm optimization are successfully used to distribute items in production systems, but also to find optimal routes or cycle times in flow storage cells.
The model for this is the “ant colony optimization” (ACO). This is a familiar approach within swarm intelligence that has many variations. Modelled on nature: How do ants find the shortest route to a source of food? They all start from the same point, the nest, and take different routes to the food. All of them leave scents, i.e. pheromone markers, on their way. More ants travel faster on the shortest route and leave more pheromones along it than on the longer routes. More pheromones attract more ants. So although the knowledge of the individuals is limited, their small contribution serves the intelligence of the swarm and optimizes its behavior.
Route planning with the help of virtual ants
Fraunhofer IPA has developed a modified approach inspired by the ACO algorithm that optimizes the total distance travelled for all mobile robots, even those from different manufacturers, in a specific environment. The approach requires the current locations of the robots to consider as many options as possible and assign tasks intelligently. And, of course, it doesn’t work with pheromones like the ants do. Instead, each individual robot sends “virtual ants” out to all the destinations to which the robots could travel. The ants travel to the destinations, and die if they collide with other ants in the process. In the end therefore, only the ants that have successfully reached their destination and delivered the virtual object survive.
The real robots can then use this information to plan their route correctly. At the same time, not every robot is assigned a task if other options are more favorable. After several cases were tested with the algorithm, the optimization for the total distance travelled by all robots resulted in a minimal plan whereby a mobile robot was assigned no tasks, and therefore saved a useless trip.
In addition to the work in SE.MA.KI, Fraunhofer IPA is working on incorporating heterogeneous mobile robots into the concept. This allows mobile systems with different capacities, such as autonomous tugger trains and mobile robots with a manipulator, to work in the same environment and also be intelligently scheduled. The vision that inspires this work is the full orchestration of heterogeneous mobile robots that can perform a range of tasks optimally in a matrix production environment.
Matrix production series
A series of articles on “interaktiv online” focuses on matrix production, a flexible production system that increases a company’s resilience and ability to change. Already published in this series is:
- Kein Fehler in der Matrix by Daniel Ranke
- Zuverlässige Durchlaufzeitprognose in der Matrix by Lisa Charlotte Günther
- Automatisierte Prozesskontrolle in der Matrix by Hang Beom Kim and Timo Leitritz
- Selbstlernende Roboter – die matrixfähige Montagezelle by Arik Lämmle
- Prozessablauf zur Rekonfiguration von Matrix-Produktionssystemen by Michael Trierweiler
- Maschinelles Lernen ermöglicht matrixfähige Kommissionierzelle by Felix Spenrath and Richard Bormann
- Autonome Auftragssteuerung mit Reinforcement Learning by Tobias Heinrich Nagel
- Fertigungsrelevante Informationen in 2D-Zeichnungen automatisch erkennen und verarbeiten by Christoph Haar and Hang Beom Kim
- Die Materialbereitstellung kostenoptimal und adaptiv planen by Daniel Ranke
This article was written in the context of “SE.MA.KI” (Selbstlernende Steuerung einer technologieübergreifenden Matrixproduktion durch simulationsgestützte KI). The research and development project SE.MA.KI. is funded by the German Federal Ministry of Education and Research (BMBF). Support code: L1FHG42421. The responsibility for the content of this publication lies with the author.
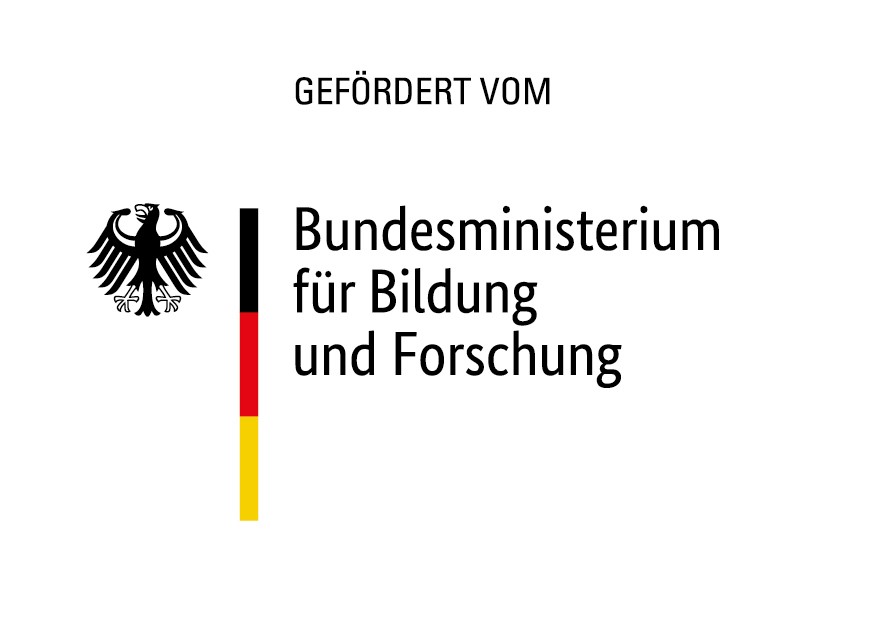
Contact
Tobias Rainer Schäfle
Business segment manager automated manufacturing systems
Phone: +49 711 970-1469