Quelle: Fraunhofer IPA/Grafik: Andrine Theiss
Die Materialbereitstellung kostenoptimal und adaptiv planen
In der Matrixproduktion muss das Material zuverlässig und kostengünstig genau dort ankommen, wo es benötigt wird. Doch wie ist das bei der hohen Dynamik und den Freiheitsgraden möglich? Um diesen Herausforderungen zu begegnen, wird ein Planungsvorgehen mit der Integration einer Simulation und eines Auswahl-Algorithmus entwickelt.
Veröffentlicht am 20.10.2022
Lesezeit ca. 5 Minuten
Die Materialbereitstellung steht unter dem Druck, alle benötigten Teile rechtzeitig an den entsprechenden Ort in der Produktion zu bringen. Fehlteile führen zu Produktionsunterbrechungen – und die sind teuer. In der Matrixproduktion steigen die Anforderungen an die Bereitstellung, da im operativen Betrieb mehr Freiheitsgrade zur Auftragsverteilung bestehen. Wenn die Auftragssteuerung erst zum spätest-möglichen Zeitpunkt definiert, an welcher Station der Auftrag bearbeitet wird, kann die Materialbereitstellung gegebenenfalls nicht mehr rechtzeitig reagieren. Gleichzeitig gilt das Grundziel, die Kosten in der Bereitstellung möglichst gering zu halten.
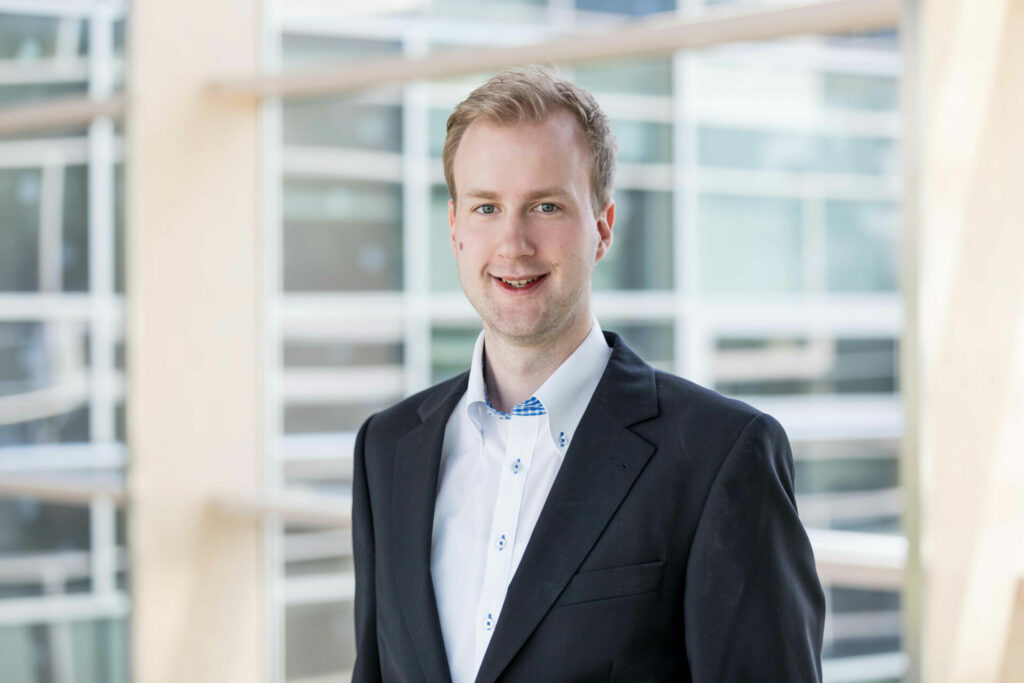
Die logistischen Ziele der Materialbereitstellung sind also
- die sichere Versorgung der Stationen mit Material, trotz der Dynamik in der Matrixproduktion,
- der Umgang mit der Zuweisung von Aufträgen an Stationen zum spätest-möglichen Zeitpunkt,
- die kostengünstige Bereitstellung und
- die Entlastung des Planers bei der Auswahl des geeigneten Materialbereitstellungssystems.
Wie ist eine solche Materialbereitstellung also zu planen? Und was ist im Speziellen in Bezug auf die Matrixproduktion zu beachten?
Automatisierte Planung der Materialbereitstellung mit logistischer Kostenminimierung
Mit diesen Fragen beschäftigen sich Wissenschaftlerinnen und Wissenschaftler im Forschungsprojekt »Selbstlernende Steuerung einer technologieübergreifenden Matrixproduktion durch simulationsgestützte KI« (SE.MA.KI). Ihre Forschungsarbeit teilt sich in zwei Bausteine auf: Simulation und Auswahlentscheidung. Der zeitliche Horizont der Planung ist auf einer taktischen Ebene. Es werden Zeiträume von wenigen Wochen bis Monaten betrachtet.
Der Baustein »Simulation« greift die Herausforderung auf, dass Matrix-Produktionssysteme sich stark dynamisch verhalten und Nachfragemengen je Station unsicher sind. Um diese Unsicherheit zu reduzieren, wird die geplante Matrixproduktion in einer Simulationsumgebung abgebildet. Mit diesem digitalen Abbild werden im nächsten Schritt Simulationsexperimente durchgeführt, um das dynamische Verhalten zu untersuchen. In jedem Experiment werden aus einer festgelegten Stückzahlverteilung unterschiedliche Plan-Aufträge eingesteuert. Zu jedem Experiment werden die an den Stationen aufgetretenen Materialverbräuche mitgezählt.
Nach einer definierten Anzahl an Experimenten wird die Simulation beendet und über alle Experimente die beobachteten Verbräuche ausgewertet. Aus der Vielzahl an Experimenten kann ein realistischer Verbrauchswert abgeleitet werden, der für die weitere Planung verwendet wird. Die Simulation reduziert die planerische Unsicherheit, gibt dem Planer Einsicht in das dynamische Verhalten der Matrixproduktion und macht die Matrixproduktion damit auch beherrschbar.
Aus den in der Simulation bestimmten Verbrauchswerten werden zu erwartende Kosten für alternative Materialbereitstellungsstrategien abgeleitet. Eine Materialbereitstellungsstrategie ist beispielsweise die Kanban-Bereitstellung, die Auftragskommissionierung oder die periodische Bereitstellung. Für jedes Material an jeder Station muss nun entschieden werden, welche Bereitstellungsstrategie die vorteilhafteste ist, um eine stabile und kostengünstige Versorgung sicherzustellen. Zu berücksichtigen ist, dass auch logistische Restriktionen (wie begrenzte Fläche) abgebildet werden müssen und die Auswahl beeinflussen. Dadurch ist die Auswahl nicht trivial und wird im Baustein »Auswahlentscheidung« betrachtet.
Die Informationen zu Verbrauchswerten, Flächenverhältnissen und dergleichen mehr werden zunächst aufgenommen und in eine mathematische Problembeschreibung überführt. Diese soll entsprechend optimal gelöst werden. Dazu haben die Forscherinnen und Forscher im Projekt SE.MA.KI unterschiedliche mathematische Lösungswege untersucht und einen geeigneten Algorithmus ausgewählt.
Webinar zur Matrixproduktion
Abschied vom Fließband: Die modulare Matrixproduktion ist adaptiv konfigurierbar, Anlagen und Stationen passen sich an neue Stückzahlen und Varianten an. Produkte durchlaufen nur die auftragsspezifisch benötigten Prozesse. Im kostenfreien Webinar »Matrixproduktion – Wandlungsfähige und resiliente Produktionssysteme« am 24. November 2022 erfahren Sie mehr über die Potenziale und Umsetzungsmöglichkeiten von Matrix-Produktionssystemen.
Dabei ist es wichtig, dass der Algorithmus zur Problemstellung passt und in möglichst allen Unternehmen angewendet werden kann (indem beispielsweise keine besondere Hardware verwendet werden muss). Das Forschungsteam stützt sich dabei auf eine klassische mathematische Beschreibung und einen Algorithmus, die beide sogar in Excel abgebildet werden können. Um die Leistungsfähigkeit zu steigern, haben die Wissenschaftlerinnen und Wissenschaftler zusätzlich in Python ein Programm geschrieben, das die Berechnungen schneller durchführt. Über ein entsprechendes Interface können alle Informationen übertragen und ausgetauscht werden. Mit dieser Software kann nun automatisiert und binnen weniger Sekunden bis Minuten die geeignete Bereitstellungsstrategie bestimmt werden.
Die beiden sequenziell ablaufenden Bausteine »Simulation« und »Auswahlentscheidung« erlauben es, die Planung der Materialbereitstellung kurzzyklisch und parallel zu anderen Tätigkeiten eines Planers oder einer Planerin durchzuführen. Die Vorteile sind:
- Planerinnen und Planer sind nicht lange an die Aufgabe gebunden.
- Das Ergebnis ist kein ungefähres Bauchgefühl, sondern mathematisch nachvollziehbar.
- Die Planung kann häufig durchgeführt werden.
Somit ist das Vorgehen auch adaptiv anwendbar, wenn sich Eingangsgrößen ändern. Unsere eingangs aufgezeigten Ziele sind mit den zwei Bausteinen erfüllt. Die Materialbereitstellung kann sicher und zuverlässig für die Matrixproduktion geplant werden.
Ein weiterer Vorteil und Nebeneffekt: Der Ansatz aus Simulation und Auswahlentscheidung kann auch in klassischen Produktionssystemen wie der Linie oder Box-Montage angewendet werden. Für die Simulation muss nur das spezifische und reale Produktionssystem abgebildet werden und für die Auswahlentscheidung wird die mathematische Beschreibung angepasst oder sogar vereinfacht. Das methodische Vorgehen und die Softwaretools bleiben gleich.
Serie zur Matrixproduktion
Eine Serie von Beiträgen beschäftigt sich auf interaktiv online mit der Matrixproduktion, einem flexiblen Produktionssystem, das Resilienz und Wandlungsfähigkeit eines Unternehmens erhöht. Erschienen ist in dieser Serie bereits:
- Kein Fehler in der Matrix von Daniel Ranke
- Zuverlässige Durchlaufzeitprognose in der Matrix von Lisa Charlotte Günther
- Automatisierte Prozesskontrolle in der Matrix von Hang Beom Kim und Timo Leitritz
- Selbstlernende Roboter – die matrixfähige Montagezelle von Arik Lämmle
- Prozessablauf zur Rekonfiguration von Matrix-Produktionssystemen von Michael Trierweiler
- Maschinelles Lernen ermöglicht matrixfähige Kommissionierzelle von Felix Spenrath und Richard Bormann
- Autonome Auftragssteuerung mit Reinforcement Learning von Tobias Heinrich Nagel
- Fertigungsrelevante Informationen in 2D-Zeichnungen automatisch erkennen und verarbeiten von Christoph Haar und Hang Beom Kim
Dieser Artikel ist im Rahmen von »SE.MA.KI« (Selbstlernende Steuerung einer technologieübergreifenden Matrixproduktion durch simulationsgestützte KI) entstanden. Das Forschungs- und Entwicklungsprojekt SE.MA.KI. wird vom Bundesministerium für Bildung und Forschung (BMBF) gefördert. Förderkennzeichen: L1FHG42421. Die Verantwortung für den Inhalt dieser Veröffentlichung liegt beim Autoren.
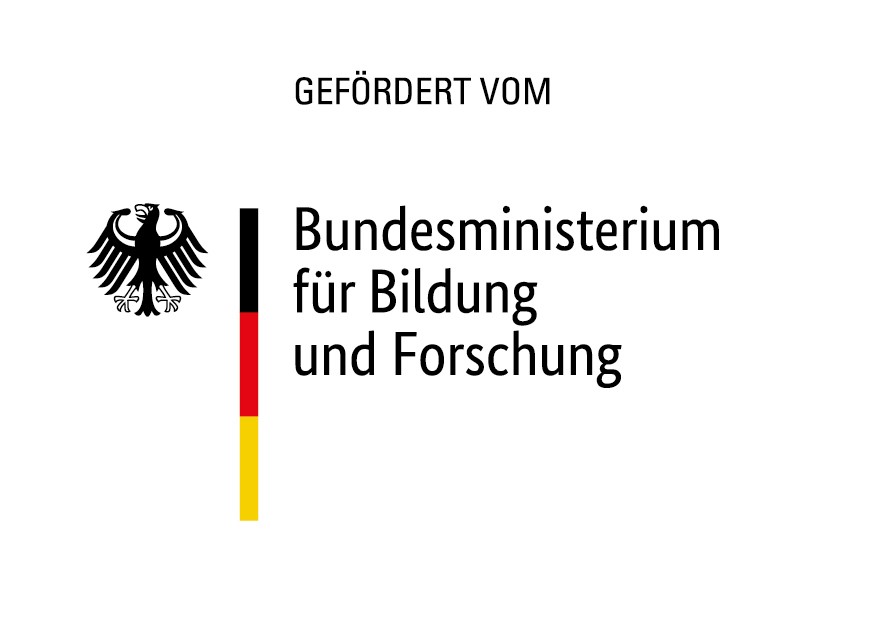
Ihr Ansprechpartner
Daniel Ranke
Geschäftssegmentleiter End-to-End-Prozesse
Telefon: +49 711 970-1134