Michael Scholz at the Karlsruhe plant of Siemens AG. (Source: Fraunhofer IPA/Photo: Rainer Bez)
Go with the flow: Matrix production in the flow
Fraunhofer IPA and Siemens AG in Karlsruhe operate the “Matrixproduktion im Fluss” (matrix production in flow) lab. The aim is a comprehensive transformation of the manufacturing structure into matrix production. In an interview, the two project leaders provide insights into their work to date.
Published on 2023-04-20
Reading time roughly 9 minutes
With around 1000 employees, the Karlsruhe site is one of the largest Siemens AG plants in Germany and the largest plant for industrial PCs in the group. The vertical range of manufacture covers almost all the stages of electronics production: On the one hand, Siemens assembles and tests flat modules. On the other, a wide range of products is assembled, inspected and tested in Karlsruhe, from automation systems, process control systems and industrial PCs to industrial communication and object identification, process control systems and industrial PCs to industrial communication and object identification. The site was named “Factory of the Year” in 2021.
Siemens has initiated a comprehensive process of digital transformation at the Karlsruhe plant to meet the increased market demands for flexibility and quality, to improve competitiveness in a global comparison and to meet increasingly complex customer requirements. Fraunhofer IPA has been supporting this transformation in various projects since September 2019. A long-term development cooperation was agreed in early 2022 and a “lab project” was set up to be completed in December 2024 to work on the many interdisciplinary topics. The focus of the lab cooperation is matrix production with the associated topics: “the human being at the centre” and “lean production”.
In an interview with interaktiv, the two project managers Michael Scholz (Siemens) and Michael Trierweiler (Fraunhofer IPA) explain how the new plant strategy is being jointly implemented at the Siemens site in Karlsruhe.
Mr. Scholz, as early as summer 2019, the "Handelsblatt” (a German-language business newspaper) ran the headline: “The quiet farewell to Henry Ford”. What was meant by this was a move away from the assembly line and towards matrix production systems. Why will your plant no longer rely exclusively on highly specialised production lines in the future, but will add matrix-structured concepts?
Michael Scholz: This is mainly due to our very high product variance. We would require a large number of lines if we wanted to retain the standard line structure and, in so doing, would have a high investment requirement and would therefore be unable to manufacture the product in a cost-effective way. Moreover, the products we produce require a high level of automation. Flat modules in electronics production are assembled in a highly automated process.
Matrix production as we experience it is what we call “matrix production in the flow”. It enables very high product variants and volumes, as each individual matrix section can process any product. We invest in a specific number of plants and then use the plants in a highly flexible process. This means that, when you look at it from the outside, the production resembles workshop production. This would be one step ahead of Henry Ford. But we insert a virtual flow into this layout to remain in the one-piece flow. We adopt this important element of Henry Ford’s “lean production”. This way, we combine the best of both worlds: the flexibility of the fixture-oriented organisation and the productivity of lean production.
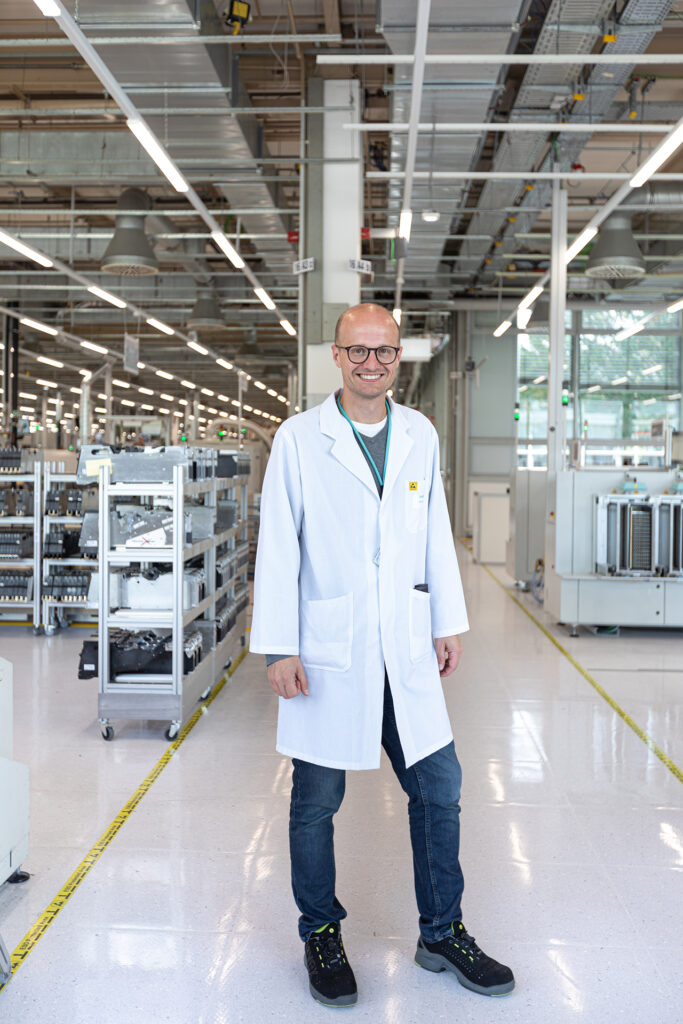
Michael Scholz, Head of Engineering Industry PC in the Karlsruhe production plant of Siemens AG, combines matrix and lean. One of his roles at Siemens, was as a project manager for the digital connection of the SMT production facilities and the physical networking of such systems with autonomous, mobile transport robots to form a highly flexible matrix production. Scholz uses his mechanical engineering expertise to create the prerequisites for sustainable production with digitalization and value creation through adaptable production systems.
Mr. Trierweiler, what role does Industrie 4.0 play in matrix production systems?
Michael Trierweiler: It plays a crucial role. This is because the virtual flow connecting the individual production modules in matrix production is only possible using the technologies of Industrie 4.0. Data must be permanently collected and optimisation decisions taken in real time based on this data to make this process as efficient as possible. Control commands must then be sent to the process modules and to the automated guided vehicles (AGVs) to execute the material transports. Digital assistance systems also support workers and managers. This requires, among others, end-to-end networking, which was developed in the context of Industrie 4.0.
Mr. Scholz, was it difficult to take your employees along on the journey to a new production system?
Scholz: Individual implementation steps were difficult. But what is particularly important to us is that the digital factory only becomes intelligent through people, and that’s why we have a transformation team that has taken the employees with them. Numerous concerns have been addressed, and many have wanted to help shape the transformation themselves. Example: Our employees have given names to the automated guided vehicles (AGVs), which makes the vehicles part of the team. Our AGVs are called “Wicki und die Starken Männer” (Wicki and the Strong Men). This turns our robots into colleagues, who also sometimes make mistakes and need help.
Mr. Trierweiler, what is the aim of the lab cooperation between Siemens and the Fraunhofer IPA?
Trierweiler: Our common goal is to pursue the continuous further development of the plant. To this end, the Fraunhofer IPA contributes interdisciplinary know-how and personnel capacity. To date, these have mainly been colleagues from production management, digitalisation and automation. For example, we can also provide the infrastructure to set up demonstrators if required.
Mr. Scholz, can you report on the first results and perhaps also solutions that have been developed in the lab?
Scholz: The exciting thing about the lab is that: We work in tertial schedules. Each project must have achieved a defined goal within four months, which enables us to we generate results every four months that have a direct impact on our factory targets. A great example of this is the “mini matrix”. In the project we tested a matrix system in a highly automated final assembly. That’s where we lifted the AGV shuttles to table level, which transport the products between the production stations as free-moving workpiece carriers with no belt. We simulated the process with the Fraunhofer IPA and were thus able to determine the design and limit capacity.
Mr. Trierweiler, can the results from the lab simply be transferred to other companies or is a matrix production system always designed precisely for the product to be manufactured?
Trierweiler: Firstly, the initial situation and the problem differ in each application, for example, does this concern manufacturing or assembly operations or is it also about the key figures to which the production system is to be optimized. However, the principles we use in the design of matrix production systems are always the same – modularisation paired with an optimised flexible material flow. This is precisely what enables high flexibility in daily operations combined with high productivity and the option to reconfigure in the scheduled period. In detail, this always leads to application-specific solutions, but the basic knowledge and experience can be transferred.
Are matrix production systems also valuable to small and medium-sized enterprises?
Trierweiler: Absolutely, because the demand for flexible and adaptable production systems is particularly high in SMEs. In addition, the constantly increasing cost pressures demand high productivity, and this is what matrix production systems can offer. However, SMEs are still put off by the allegedly high investments. Our conversations with SMEs show that many still believe that matrix production systems can only be introduced by corporations with large development departments, but this is simply not the case. The topic can be approached step by step and therefore with manageable outlays and risks. As a public research institute, we need to do more educational work and transfer knowledge in this area.
Mr. Scholz, the Siemens plant in Karlsruhe was named "Factory of the Year". What is there to optimize anyway?
Scholz: The following quote immediately comes to mind: “Whoever stops getting better has already stopped being good”. We constantly question ourselves and try to become a little bit better every day and to optimise our processes. We certainly haven’t exhausted our ideas.
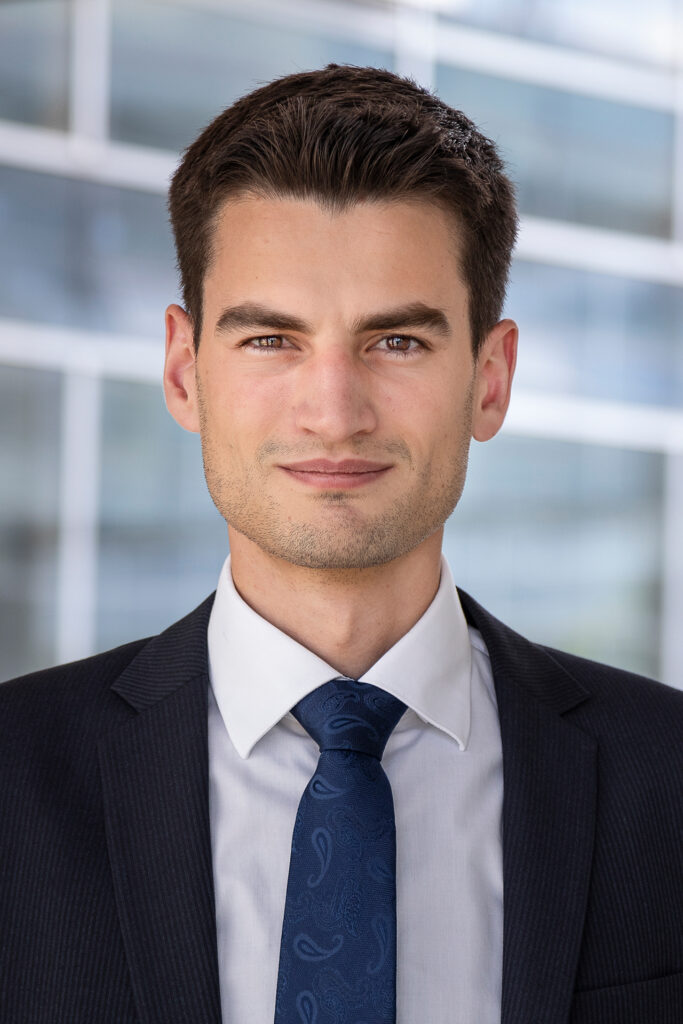
Michael Trierweiler studied mechanical engineering and has been at Fraunhofer IPA since 2018. As a project manager, he conducts application-oriented research in assembly system design, digital transformation in assembly and, most importantly, matrix assembly. In mid-2022, he and some other Fraunhofer colleagues published the study “Umsetzung von cyber-physischen Matrixproduktionssystemen” (Implementation of cyberphysical matrix production systems). In his dissertation, he develops a methodology for the permanent reconfiguration of matrix productions to constantly adapt them to changing requirements.
Was the cooperation with the Fraunhofer IPA also a factor in the award?
Scholz: Definitely. These initiatives from outside are precisely what are needed. Even the critical ones! The scientists at Fraunhofer IPA contribute disruptive ideas, some of which are far ahead of what we can implement directly, but which always provide new impetus. They take a fresh look at issues that we ourselves had ceased to question. That’s exactly how it was with matrix production: We need initiatives and fresh approaches from research to abandon belts and schedules.
Your expert contact
Susann Kärcher
Head of Assembly planning
Phone: +49 711 970-3838