Powerful and healthy, thanks to high tech
Many activities overstrain the human body and lead to wear and tear and damage in the long run. For about a decade, Fraunhofer IPA has been developing exoskeletons, i.e. support structures that protect against damage to health.
The film “Terminator” with Arnold Schwarzenegger as a cyborg was an unexpected success in 1984. The connection between man and machine stimulated the imagination. Reality is more down to earth – but no less exciting. Experts speak of ‘exoskeletons’ or ‘exosuits’. These are supporting structures that one can pull on like a suit, in order to compensate for weak areas, to make people more productive and to protect them from injuries due to overloads. Half a century ago, the American military was working on an exoskeleton that would have enabled soldiers to march for hours with heavy packs. Medicine is now also benefiting from this technology, which enables paralyzed people to walk again with the help of the exoskeleton support.
The Fraunhofer IPA has been developing exoskeletons for about a decade. It focuses on protecting the health of workers in factories and workshops. Many activities, such as overhead work, overwhelm the body, leading to injuries and disorders in the long run. Musculoskeletal disorders are the main cause of the work disability in Germany. Roboter haben zwar in den vergangenen Jahren für Erleichterung gesorgt, doch diffizile Arbeiten, bei denen Fingerfertigkeit und Kreativität gefragt sind, müssen noch immer von Menschen erledigt werden. “It has become apparent that human flexibility is not that easy to replace,” says Mark Tröster, research associate in the Physical Assistance Systems and Smart Sensors group in the Biomechatronic Systems Department at Fraunhofer IPA. In addition, demographic change ensures that older employees are becoming increasingly indispensable. Active and passive aids are available to maintain good health through to retirement age.
Passive support function
The passive exoskeleton, which has no drives, has already proven itself in practice. It is even prescribed for some activities. Different variants are available depending on the requirements. There is for instance a system for overhead work that can be strapped on like a backpack. It provides support to the arms. It is very comfortable to wear, due to its weight of about two kilograms. Und wer das Exoskelett momentan nicht benötigt, kann die Arme problemlos nach unten drücken, während die Gegenkraft stetig abnimmt. Another system that helps lift heavy loads extends below the knee. This not only supports the worker’s back, but also uses a mechanical trick to force the wearer to kneel when he leans forward. This prevents unhealthy lifting from the hips.
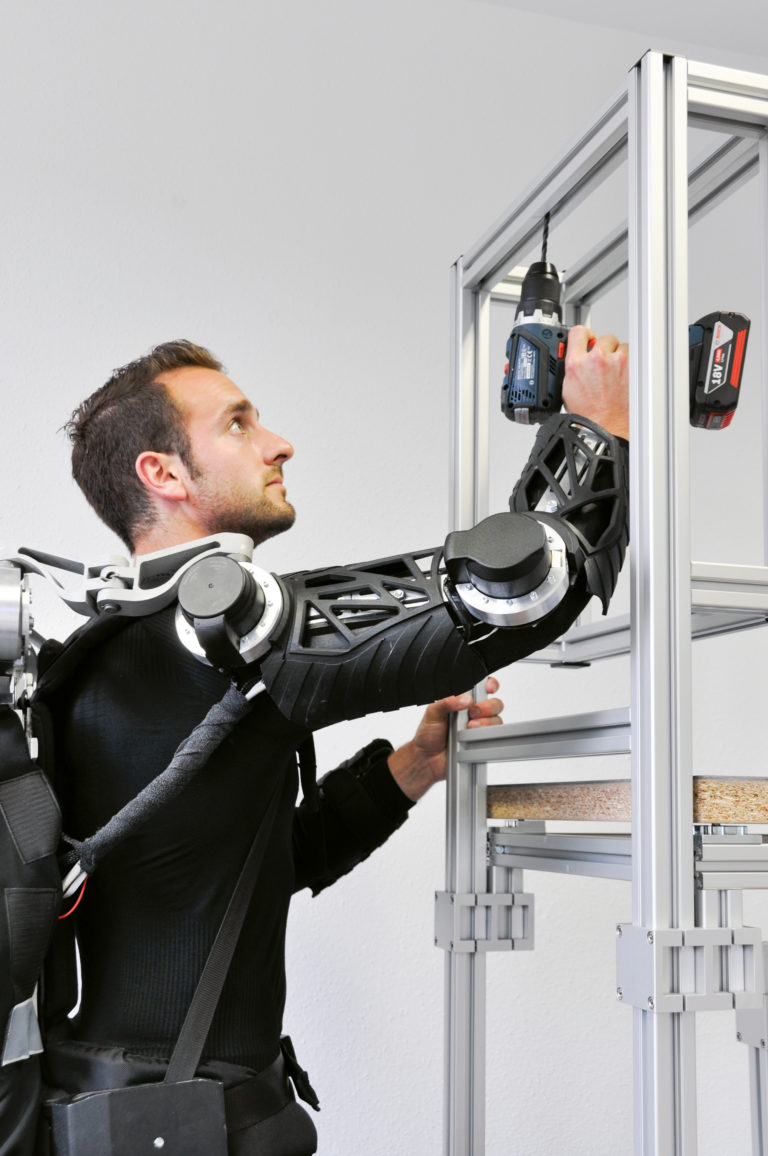
Active suppport
Actively-driven exoskeletons are more demanding. They are currently at the start of market entry. They increase muscle strength using electric motors, among other things. Dies erfordert einen nicht zu unterschätzenden technischen Aufwand, weil Aktoren, Batterien und Sensoren nötig sind. Above all, the machine has to know when to start its motors. This is by no means a trivial thing. Current research focuses on how a system automatically determines how heavy a load is, and when it should be lifted. Various motion and biosignal sensors are investigated for this purpose. This leads to the fact that electrical signals are read out in the nerves that lead to muscles. Thus, the machine becomes, so to speak, part of the body. It is also important that the support structure does not hinder the wearer when there is no work to be done. The exoskeleton should follow the wearer’s movements as if it weren’t there.
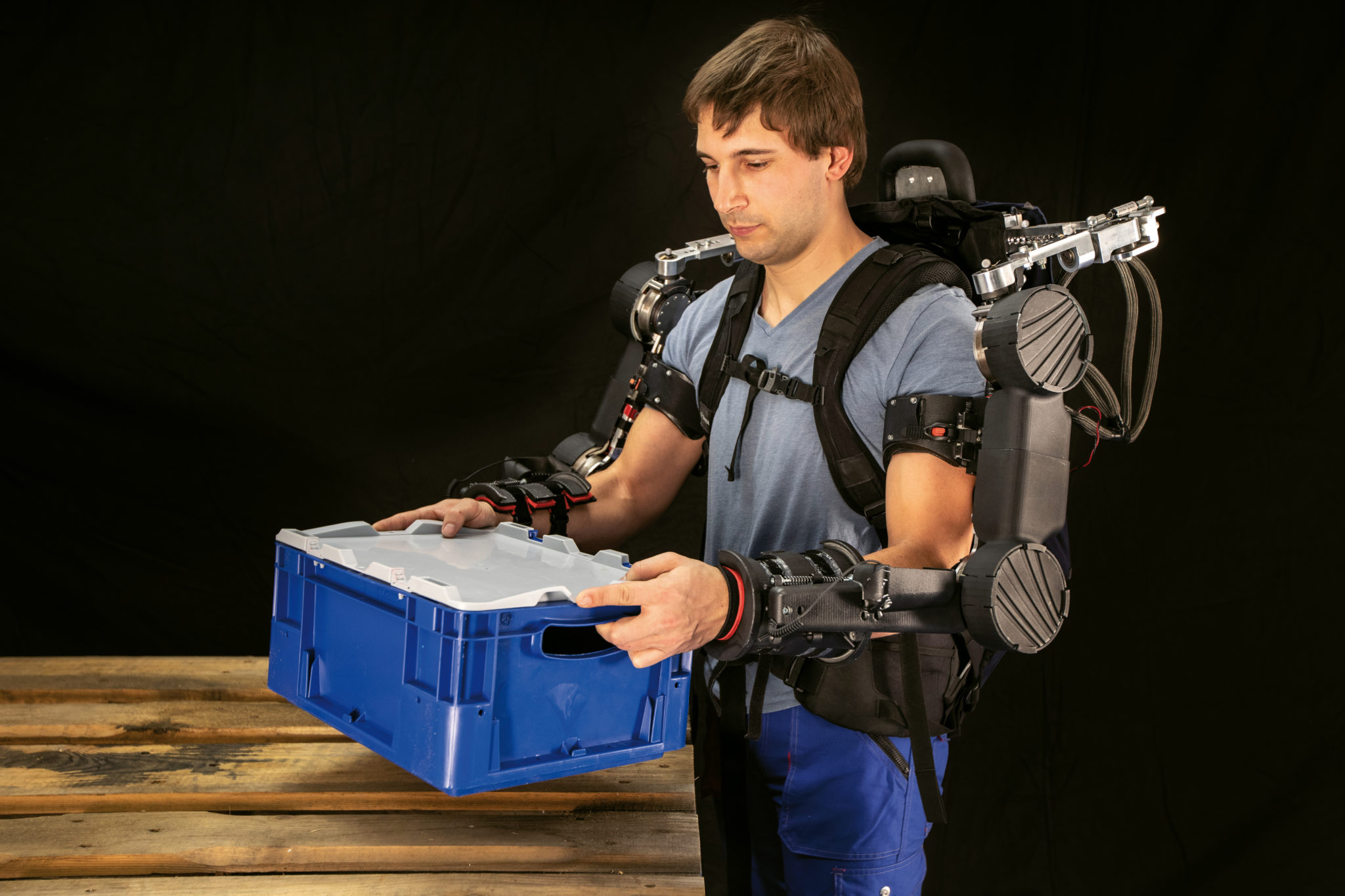
Stuttgart Exo-Jacket 2.0
The IPA team has developed the “Exo-Jacket”, which largely meets these requirements. As the Exo-Jacket actively supports arms and shoulders, and supports the back, this helps in handling loads. No one will become Superman with this system. It is focused on making it easier to lift, hold and carry loads that could be mastered without support. The employee should still definitely feel his muscles. The support system with four drives tries to compensate for up to half the weight of the load being handled. It is important that the ergonomically justifiable maximum weight, as per the German Load Handling Ordinance, is always adhered to. This research prototype is, however, still too heavy for everyday use. Tröster: “Its weight plays a major role in acceptance.” The weight of the device could however still be reduced by a few kilos with consistent lightweight construction.
Ergonomic analysis of work processes
It is not easy for a company to decide whether an activity overwhelms its employees, and to find the optimal solution. Members of the IPA team can help here. They first assess whether work processes can be changed in order to optimize employees’ activities. Sometimes, organizational or technical changes are sufficient, such as workplace rotation, lifting worktables, or rotating workpieces for machining. If this is not possible, the Stuttgart specialists measure employees’ movements directly at the site and feed the data into a kinetic human model. Loads in every joint and muscle can then be calculated to decide which exoskeleton is appropriate. The IPA crew has already set their sights on a special application: As part of the BMBF ExoPflege research project, they want to develop a comfortable and active exoskeleton in cooperation with three companies that will make it easier for caregivers to move unconscious or anesthetized patients from one bed to another.
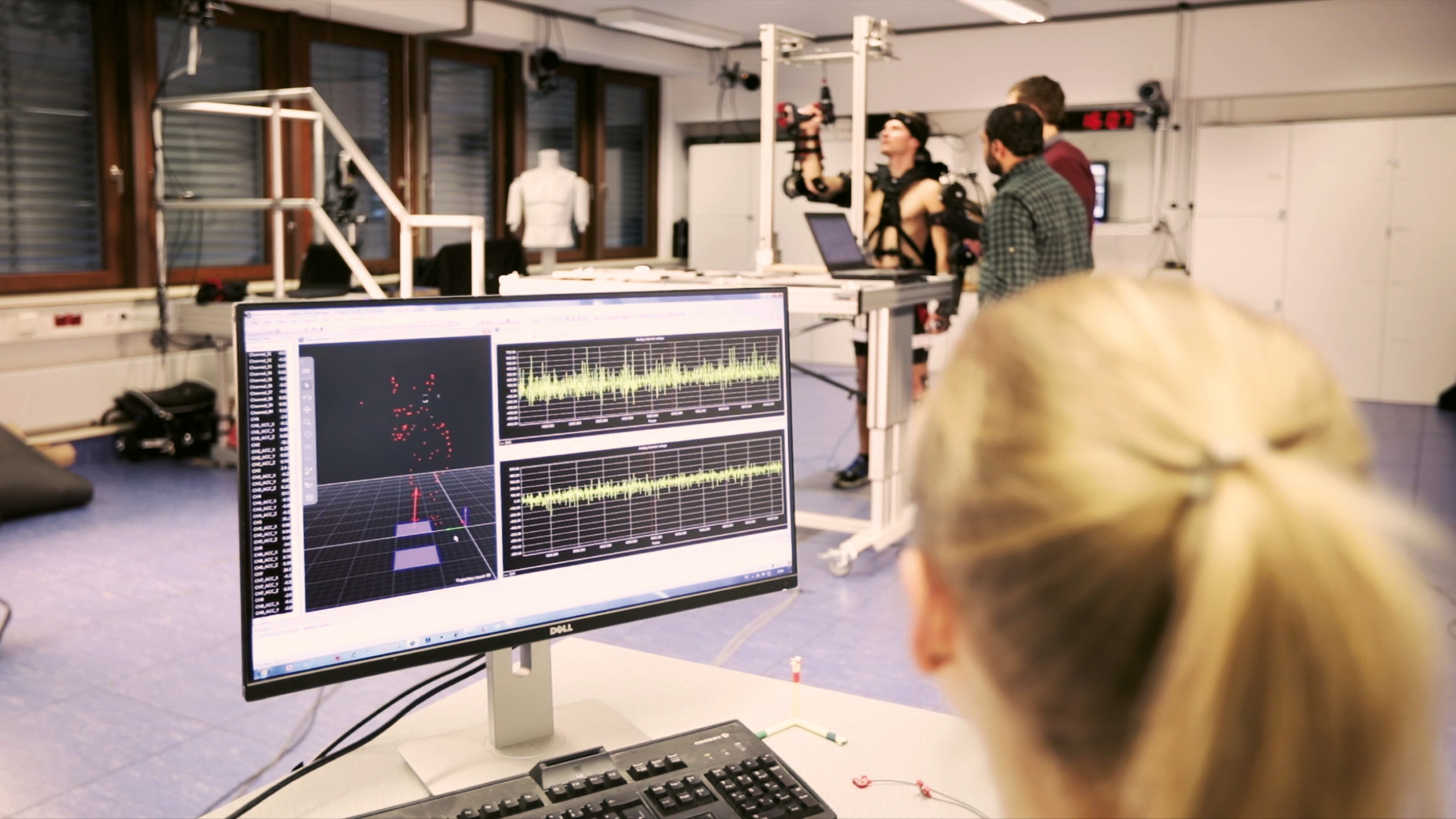
Contact
Christophe Maufroy
Research team leader Physical Assistance Systems Engineering
Phone: +49 711 970-1167