Quelle: Fraunhofer IPA/Foto: Rainer Bez
Auftragsmanagement im Quick Check
In einem Quick Check ermitteln Hans-Hermann Wiendahl und sein Team die Stärken und Schwächen der Planungs- und Steuerungsprozesse der Auftragsabwicklung und der Lieferkette inklusive der IT-Werkzeuge. Dieser Ansatz bewertete bei der Breyer GmbH Maschinenfabrik Stärken und Schwächen in der Auftragsabwicklung und leitete ein Vorgehen ab, mit dem Breyer seine Planung und Steuerung der Auftragsabwicklungskette samt indirekter Bereiche schrittweise verbessern kann.
Für Produktionsunternehmen rücken neben Produktqualität und -preis verstärkt logistische Wettbewerbsfaktoren wie Liefertreue und -zeit sowie Transparenz in der Auftragsabwicklungskette in den Fokus von Verbesserungsüberlegungen. Die optimale Gestaltung des Auftragsmanagements wird somit zum Schlüsselelement produzierender Unternehmen.
Symptome, Ursachen und Verbesserungsmöglichkeiten (er-)kennen
Grundvoraussetzung eines optimalen Auftragsmanagements ist ein gemeinsames Verständnis der zugrundeliegenden Rahmenbedingungen sowie der Schwachstellen und ihrer Ursachen. In der Praxis fehlt dies jedoch häufig, insbesondere, weil hierauf ausgerichtete und einfach anzuwendende Analysewerkzeuge fehlen. Bestehende Methoden untersuchen oft nur Einzelaspekte wie beispielsweise Einzelverantwortlichkeiten und -abläufe, Dispositionseinstellungen oder Lieferzusageregeln losgelöst und stellen keine Zusammenhänge her. Es fehlt also eine strukturierte Kombination zur umfassenden Analyse des Auftragsmanagements für ein verständliches Gesamtbild zu Symptomen, Ursachen und Verbesserungsmöglichkeiten im Auftragsmanagement. Genau hier setzten wir mit unserem Quick Check an, der über bestehende und eigens entwickelte Analyseelemente zunächst systematisch die Einzelaspekte prüft und dann die erforderlichen Zusammenhänge für ein Gesamtverständnis herstellt.
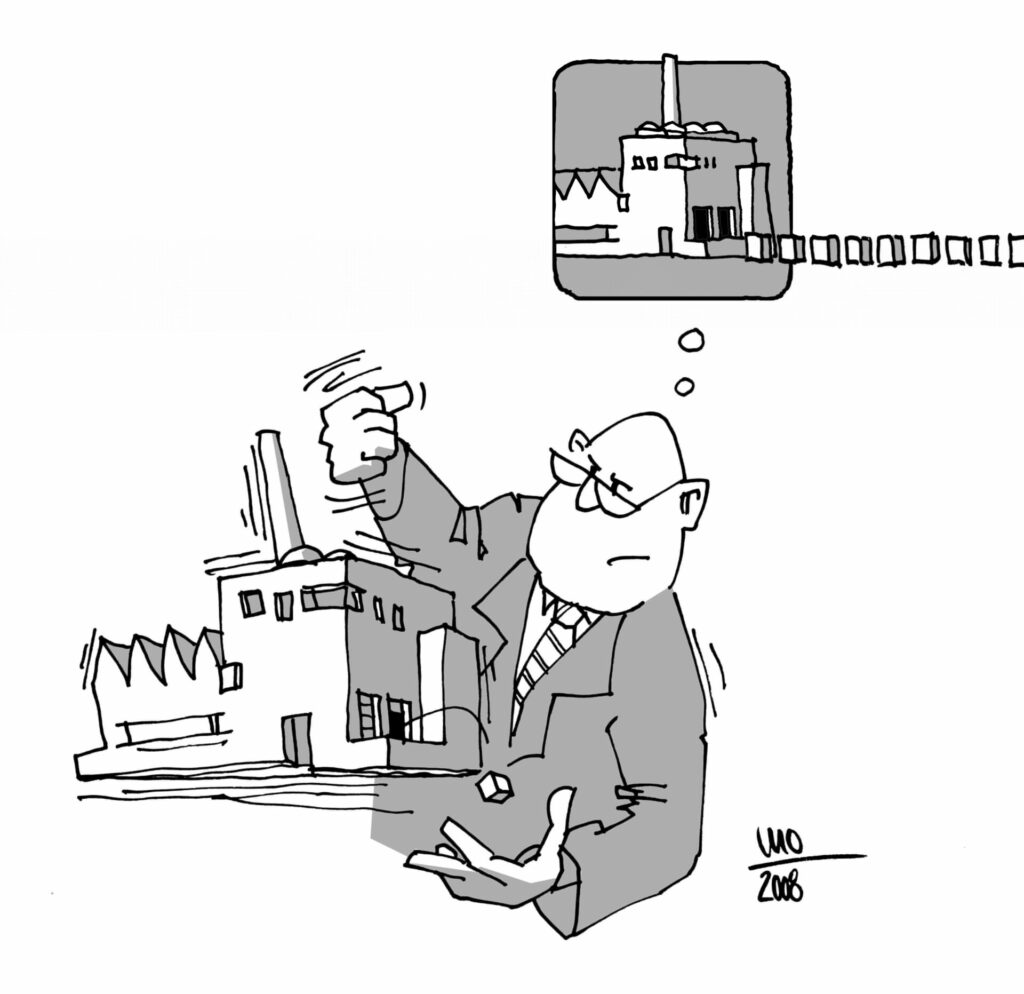
Breyer prüft Verbesserungspotenziale
Grundvoraussetzung eines optimalen Auftragsmanagements ist ein gemeinsames Verständnis der zugrundeliegenden Rahmenbedingungen sowie der Schwachstellen und ihrer Ursachen. In der Praxis fehlt dies jedoch häufig, insbesondere, weil hierauf ausgerichtete und einfach anzuwendende Analysewerkzeuge fehlen. Bestehende Methoden untersuchen oft nur Einzelaspekte wie beispielsweise Einzelverantwortlichkeiten und -abläufe, Dispositionseinstellungen oder Lieferzusageregeln losgelöst und stellen keine Zusammenhänge her. Es fehlt also eine strukturierte Kombination zur umfassenden Analyse des Auftragsmanagements für ein verständliches Gesamtbild zu Symptomen, Ursachen und Verbesserungsmöglichkeiten im Auftragsmanagement. Genau hier setzten wir mit unserem Quick Check an, der über bestehende und eigens entwickelte Analyseelemente zunächst systematisch die Einzelaspekte prüft und dann die erforderlichen Zusammenhänge für ein Gesamtverständnis herstellt.
Aus den zuvor genannten Gründen beauftragte auch die Breyer GmbH Maschinenfabrik, ein Hersteller für Extrusionsanlagen, das Fraunhofer IPA mit einem Quick Check. Stark durch historische Entwicklungen und partikuläre Verbesserungsprojekte geprägt, war das Auftragsmanagement vor dem Hintergrund zukünftiger Verbesserungsprojekte zu prüfen. Der Quick Check analysierte die Stärken und Schwächen der Planungs- und Steuerungsprozesse der Auftragsabwicklung inklusive der IT-Werkzeuge und leitete darauf aufbauend erste Lösungsideen beziehungsweise Handlungsfelder zur Verbesserung ab. Wir erarbeiteten die Ergebnisse gemeinsam mit Vorgesetzten und Fachleuten und analysierten die Ist-Situation qualitativ, ergänzt durch verfügbare Unternehmenskennzahlen. Das strukturierte Vorgehen im Quick Check erfolgte dabei in vier Schritten.
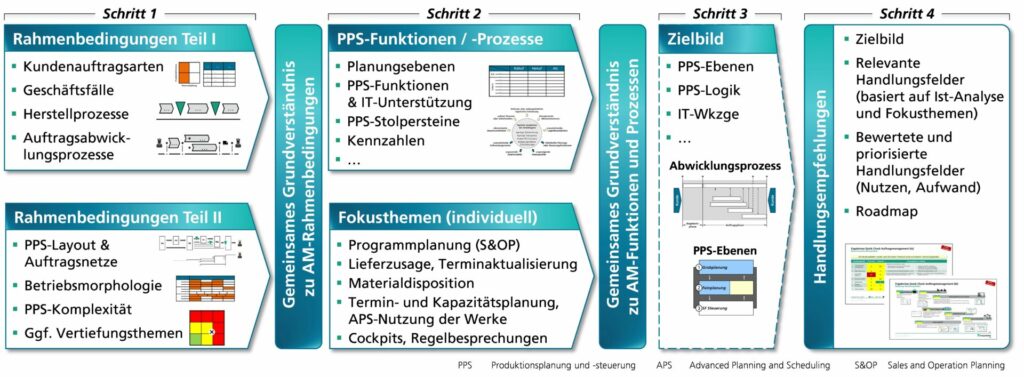
Schritt 1 nimmt die Rahmen- und Randbedingungen des Auftragsmanagements Ihres Unternehmens strukturiert auf. Ziel ist ein gemeinsames Verständnis der Auftragsabwicklungsprozesse »Kunde – Kunde« und der Herstellprozesse sowie der Geschäfts- und Abwicklungsfälle. Abgeleitet aus der Herstellkette, bilden das PPS-Layout sowie die Auftragsnetze zwei zentrale Visualisierungen: Sie beschreiben die aus der Herstellung (von Konstruktion bis Versand) und der Produktstruktur resultierenden PPS-Anforderungen. Die sogenannte Betriebsmorphologie oder die PPS-Komplexität ergänzen diese. Die Ergebnisse beschreiben die Anforderungen an das Auftragsmanagement strukturiert.
Schritt 2 erzeugt ein gemeinsames Verständnis zur heutigen Leistungsfähigkeit des Auftragsmanagements, also der Planung und Steuerung der gesamten Auftragsabwicklung. Hierzu wird die Ist-Situation mit Fokus auf den Planungs- und Steuerungsfunktionen, ihrer IT‑Unterstützung sowie ihre logischen Inkonsistenzen und Lücken (sogenannte PPS-Stolpersteine) aufgenommen. Darüber hinaus betrachtet dieser Schritt die sogenannten Fokusthemen, also die vom Unternehmen vermuteten Haupt-Schwachstellen; typische Fokusthemen sind: Programmplanung (S&OP), Lieferzusage, Materialdisposition, Termin- und Kapazitätsplanung oder nutzergerechte Cockpits (zur rollengerechten Aufbereitung der Entscheidungsinformationen).
Wichtigstes Vorgehenselement sind qualitative Analysen: Erfahrungsgemäß liefern Expertenbefragungen mit halbgeschlossenen Fragen ausreichend genaue Ergebnisse, identifizieren inkonsistente Auslegungen und schaffen außerdem über Begriffsklärungen ein gemeinsames Problemverständnis. Demgegenüber sind quantitative Analysen oft zeitaufwendig und liefern vor allem in frühen Analysephasen geringe Zusatzerkenntnisse, deshalb verwenden wir sie vor allem bei widersprüchlichen Einschätzungen oder für Detailanalysen in Fokusbereichen.
Beispielsweise stellten sich hier unterschiedliche Definitionen des Fertigstellungstermins der Beteiligten heraus: Die Montage verstand diesen Termin als »fertig montiert«, die PPS interpretierte ihn als »ab Werk«. Das erschwert eine realistische Terminplanung und -einhaltung erheblich. Ein weiteres häufiges Missverständnis war die Verwechslung von Symptom und Ursache. Hier sprachen die Teilnehmer oft von den unterschiedlichsten Problemen der Auftragsverwaltung. Es stellte sich aber meist heraus, dass sie eigentlich alle über das gleiche Problem sprachen und nur unterschiedliche Symptome einer Ursache beschrieben.
Schritt 3 formuliert, ausgehend von den angestrebten logistischen Zielprioritäten (hier: hohe Termintreue und kurze Durchlaufzeiten), ein grobes Zielbild mit Blick auf die im Fokus stehenden Gestaltungsaspekte. Die Kernidee unseres Vorgehens besteht darin, aus den Rahmenbedingungen typische PPS-Herausforderungen abzuleiten und für diese Best-Practice-Lösungen zu finden:
- In diesem Anwendungsfall des Einzelfertiges überlappen auftragsbezogene Konstruktion und Einkauf bzw. Fertigung zeitlich, dies erfordert gute Lösungen zur wachsenden Stückliste mit entsprechend transparenten Positionsstatus zum Fertigstellungsgrad.
- Demgegenüber steht ein Saisonfertiger vor der Herausforderung einer prognosebasierten Vorfertigung, um in der Hochsaison den Bedarf zu befriedigen. Das fordert gute Lösungen zur Programmplanung (S&OP) und daraus abgeleitete Dispositionsstrategien.
Schritt 4: Mit Blick auf Best Practices in den Unternehmen lassen sich nun Handlungsfelder zur Verbesserung in den Gestaltungsfeldern ableiten, hinsichtlich ihres Potenzials durch die Teilnehmenden bewerten und zu einer groben Roadmap gliedern.
Dabei zeigen unsere Erfahrungen aus zahlreichen Industrieprojekten: Typischerweise mangelt es an der Organisation und Transparenz der betrieblichen Abläufe und weniger an der Technologie (in der Produktion).
Daher ist das bereits angesprochene gemeinsame Problemverständnis über alle Beteiligten hinweg erfolgsentscheidend. Nur das ermöglicht geeignete und gemeinsam verstandene und getragene Lösungen. Im Rahmen von Industrieprojekten ergeben sich meist überraschende Erkenntnisse für die Beteiligten. So decken zum Beispiel fehlende Kommunikation Schnittstellenprobleme auf, was Transparenz schafft. Im geschilderten Projekt mit dem Extrusionsanlagenhersteller existiert nun ein Überblick über Potenziale und inhaltliche Abhängigkeiten der Maßnahmen. Das legt den unabdingbaren Grundstein für den Erfolg nachfolgender Verbesserungsprojekte.
Zusammengefasst gewinnen Unternehmen aller Größen (und insbesondere KMU) anhand des Quick Checks einen schnellen Überblick über die eigene Auftragsabwicklung inklusive Supply Chain.
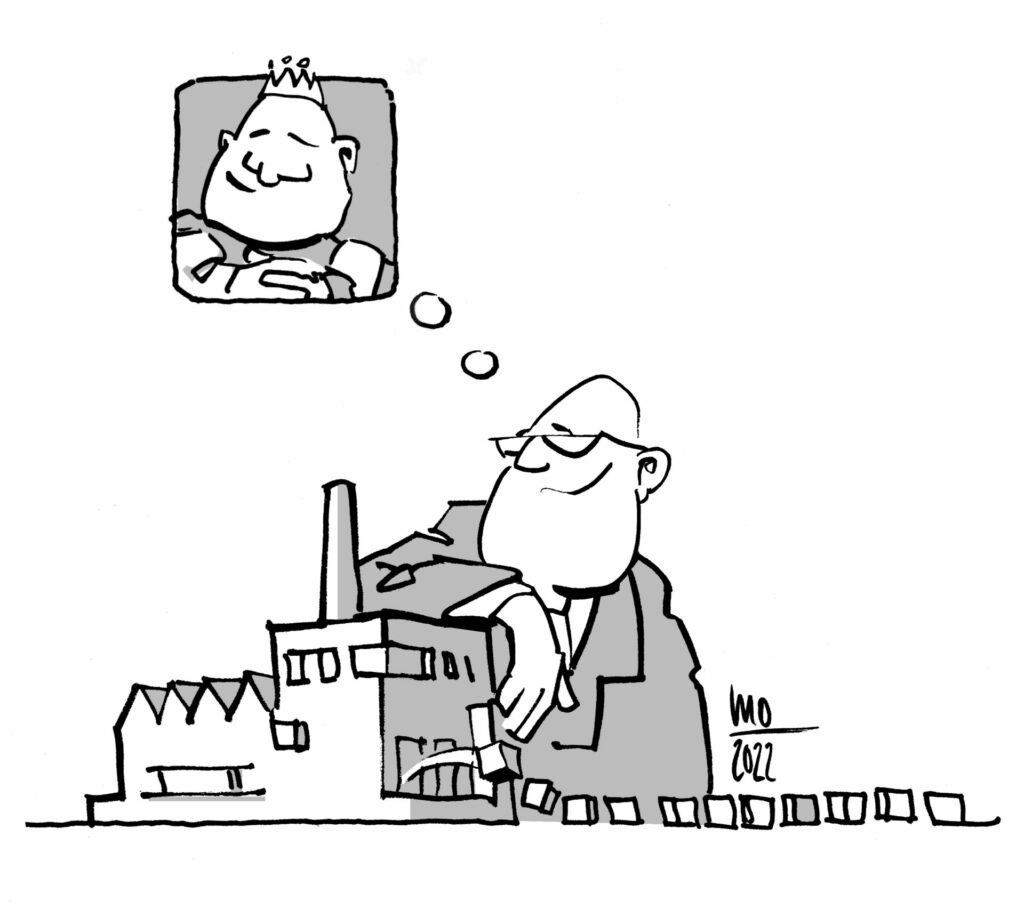
Ihre Ansprechpartner
Hans-Hermann Wiendahl
Forschungsteamleiter Digitale Auftragsabwicklung
Telefon: +49 711 970-1243
Eduardo Colangelo
Mitarbeiter des Forschungeams Digitale Auftragsabwicklung
Telefon: +49 711 970-1912