Quelle: Hindenlang GmbH
Bivalente Öfen für energieintensive Prozesse
Energie sollte man am besten dann nutzen, wenn sie billig ist. Was aber, wenn der Fertigungsprozess nicht unterbrochen werden soll? Die Lösung sind bivalente Maschinen, zum Beispiel Öfen. Sie können nicht nur unterschiedliche Energieformen nutzen, sondern auch Schwankungen im Netz ausgleichen.
Die Gussindustrie zählt zu den besonders energieintensiven Branchen. Dabei ergibt sich in Nichteisen-Metallgießereien ein spezifischer Energieverbrauch von 3,6 Megawattstunden pro Tonne, der zu 43 Prozent über Strom und zu 57 Prozent über Brennstoffe – hauptsächlich Erdgas – gedeckt wird. Durch den hohen Gesamtenergieverbrauch von 4,2 Terawattstunden besteht in der Branche das Potenzial, Schwankungen im Stromnetz signifikant auszugleichen.
In einem exemplarischen Unternehmen hat das Fraunhofer IPA daher zunächst den energieintensiven Druckgussprozess untersucht. Hier wird die Schmelze mit hohem Druck und hoher Geschwindigkeit in eine metallische Dauerform eingepresst. Der Großteil der Anlagen arbeitet im Warmkammerverfahren, wobei es auch Kaltkammeröfen gibt. Komplettiert wird der Anlagenpark durch Stanzen, Pressen und CNC-Maschinen.
Insgesamt sind 14 Flexibilitätsmaßnahmen im Detail untersucht worden. Dabei weist der Energieträgerwechsel bei den energieintensiven Technologien wie dem Tiegelofen und den Heizkühlgeräten ein besonders hohes Flexibilitätspotenzial auf, weil eine hohe flexibilisierbare Leistung und gleichzeitig eine sehr lange Abrufdauer möglich ist. Technisch umgesetzt werden kann diese Maßnahme durch die bivalente Ausgestaltung der jeweiligen Anlage, bei der der benötigte Energiebedarf dynamisch aus zwei Energieträgern bezogen werden kann. Dafür eignen sich thermische Prozessanlagen wie ein Tiegelofen besonders gut.
Bivalenter Tiegelofen
Der Tiegelofen ist im Druckgussverfahren für einen Großteil des Energieverbrauchs verantwortlich. Grundsätzlich kann ein solcher Ofen elektrisch oder mit Brennstoff betrieben werden.
Im Beispielunternehmen werden Magnesiumblöcke, sogenannte Masseln, über einen hauptsächlich manuellen Einwurf zugeführt und aufgeschmolzen. Der ursprünglich mit elektrischen Widerstandsheizelementen betriebene Tiegelofen wurde im Projekt durch einen bivalenten Tiegelofen ersetzt. Dieser kann im Betrieb dynamisch zwischen den Energieträgern Strom und Erdgas wechseln. Dieses Anlagenkonzept wurde in Zusammenarbeit mit einem Anlagenbauer für Schmelzöfen entworfen und durch thermische Simulationen optimiert.
Die Umschaltung zwischen den beiden Energieträgern Gas und Strom kann auf drei unterschiedlichen Wegen erfolgen. Neben der manuellen Auswahl des Energieträgers über die Ofensteuerung kann über ein Signal auf Hallennetzebene umgeschaltet werden. Ebenso besteht über die Hallennetzanbindung die Möglichkeit, den Wechsel, nachdem ein Signal des Stromanbieters eingegangen ist, durchzuführen. Eine Mindestdauer von fünf Minuten wird zwischen dem Wechsel der Energieträger angesetzt.
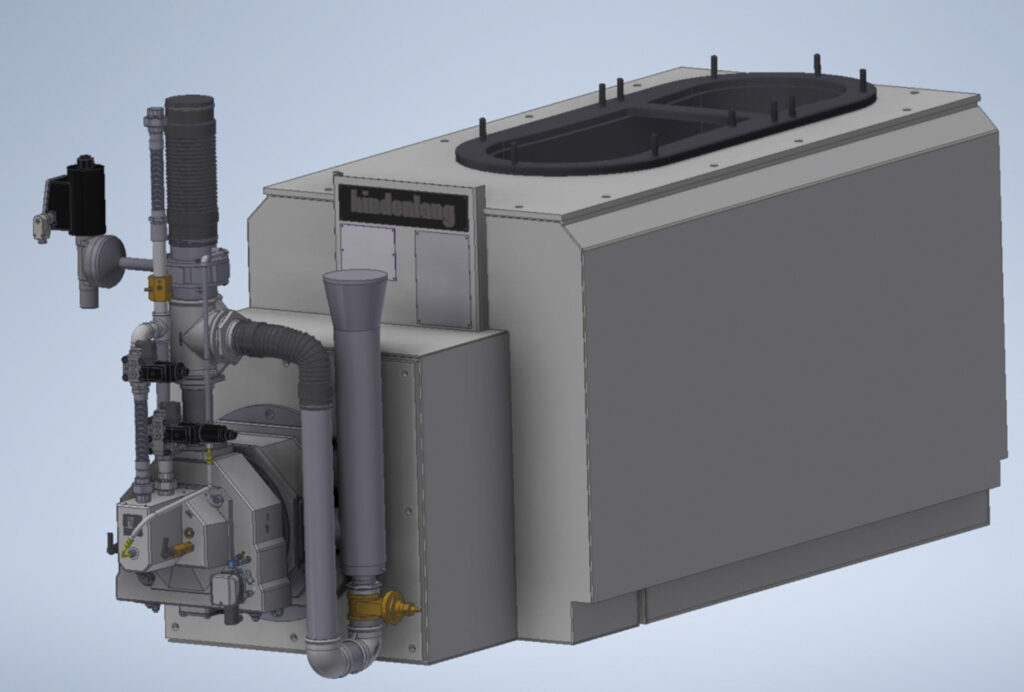
Durch den Einsatz der programmierbaren Steuerung und durch die Vorbereitung umfangreicher Schnittstellen kann das Energieflexibilitätspotenzial des Tiegelofens deutlich gesteigert werden.
Energieflexibilität durch einen Recyclingofen
In vielen Prozessschritten des bivalenten Nichteisenmetalldruckgusses fällt recycelbares Material an, beispielsweise direkt beim Druckgussprozess, beim Sägen, Stanzen und Schleifen oder in der CNC-Nachbehandlung. Im aktuellen Produktionsprozess wird das Material gesammelt und extern zum Recycling gegeben. Eine Möglichkeit, die Fertigungstiefe zu erhöhen und das Energieflexibilitätspotenzial zu steigern, bietet die Beschaffung eines eigenen Recyclingofens.
Der bivalente Recyclingkippofen im Projekt hat ein Fassungsvermögen von 1600 Kilogramm und eine elektrische Nennleistung von 250 Kilowatt sowie eine Brennerleistung von 600 Kilowatt. Das Material fällt nicht regelmäßig an, sodass das recyclingfähige Material zunächst intern im Lager gesammelt werden muss. Im Batch-Verfahren wird dann, je nach Aufkommen und Energieflexibilitätsbedarf, das Material bei einer Temperatur von 680 Grad und einer elektrischen Leistungsaufnahme von 250 Kilowatt eingeschmolzen.
Anschließend wird der Hochofen bei 175 Kilowatt mit weiterem Material beschickt – nachchargiert, sodass das komplette Fassungsvermögen vollständig genutzt und die Effizienz erhöht wird. Das Abgießen in die Masselformen benötigt vergleichsweise wenig Energie. Hier werden 75 Kilowatt zum Warmhalten benötigt. Der gesamte Prozess vom Aufschmelzen bis zum Abgießen dauert etwa acht Stunden.
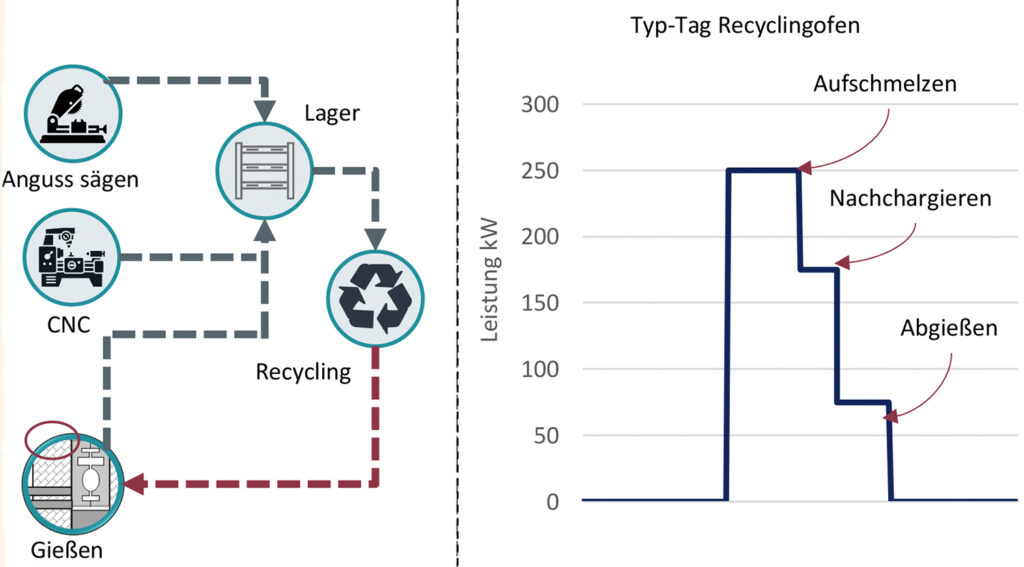
Innerhalb eines Jahres fällt so viel recycelbares Material an, dass dieser Prozess etwa 65 bis 95 Mal pro Jahr ausgeführt werden kann. Pro Batch kann der Energieträger unter den genannten Rahmenbedingungen und der Anlagenkonfiguration etwa 80 Mal gewechselt werden.
Ein Energieträgerwechsel und die Verschiebung des Auftragsstarts können also die Energieflexibilität erhöhen. Generell ist auch denkbar, die Prozessparameter anzupassen oder den Prozess zu unterbrechen. Aufgrund der bivalenten Auslegung ist dies allerdings nicht sinnvoll, da hier auch ohne Produktionsstopp und ohne Einfluss auf die Qualität die gleiche Energieflexibilität angeboten werden kann.
Die maximal flexibilisierbare Energie pro Abruf beträgt 1500 Kilowatt. Der Vorteil des bivalenten Recyclingofens liegt zum einen im höchst dynamischen Betrieb, zum anderen kann aber auch durch die Verschiebung des Auftragsstarts Energieflexibilität mit einem langen zeitlichen Horizont zur Verfügung gestellt werden.
Ihre Ansprechpartner
Alexander Mages
Mitarbeiter des Forschungsteams Sektorkoppelnde Energiesysteme
Telefon: +49 711 970-3679