Quelle: Fraunhofer IPA
Neuartiger Hybridprozess bringt hochbelastbare Leichtbau-Bauteile hervor
Für die wirtschaftliche Fertigung von hochbelastbaren Leichtbau-Bauteilen haben die Projektgruppe Prozessinnovation des Fraunhofer IPA, die Universität Bayreuth und die acad group GmbH einen zum Patent angemeldeten Hybridprozess entwickelt, der die Vorteile der additiven Fertigung und des Spritzgusses kombiniert.
Veröffentlicht am 31.03.2022
Lesezeit ca. 2 Minuten
Das kunststoffverarbeitende additive Fertigungsverfahren Materialextrusion (MEX) mit Endlosfasern ermöglicht eine Fertigung von anwendungsspezifisch ausgelegten hochbelastbaren Leichtbau-Bauteilen. Eine Fertigung von Bauteilen in hoher Stückzahl ist jedoch aktuell kaum wirtschaftlich. Der Spritzguss hingegen macht eine kostengünstige Fertigung qualitativ hochwertiger Kunststoffbauteile in hoher Stückzahl möglich. Das Potenzial für den Leichtbau ist beim Spritzgusses jedoch begrenzt aufgrund von Fertigungsrestriktionen und verfügbarer Materialien.
Ein Forschungsteam von der Projektgruppe Prozessinnovation am Fraunhofer IPA hat deshalb zusammen mit Partnern von der Universität Bayreuth und der acad group GmbH, einem Spezialisten für Engineering, Produktentwicklung und Prototypenbau für Kunststoffbauteile, in einem Entwicklungsprojekt die Vorteile beider Verfahren miteinander kombiniert. Die additive Fertigung dient dabei der Fertigung von endlosfaserverstärkten Einlegern, die eine gezielte lokale Verstärkung des Spritzgussbauteils ermöglichen. Besonderes Potenzial bietet dabei eine bezüglich der Belastungen des Spritzgussbauteils optimale Ausrichtung der einzelnen Endlosfasern im Einleger und damit im Spritzgussbauteil.
So funktioniert der Hybridprozess
Die Entwicklung des Hybridprozess zur Auslegung und Fertigung der endlosfaserverstärkten Einleger und des Spritzgussbauteils wurde anhand eines konkreten Anwendungsfalls aus der Automobilindustrie durchgeführt: Die Projektpartner fertigen mit dem neuen Verfahren eine Armlehne.
Im ersten Schritt des Hybridprozesses werden die Randbedingungen des Spritzgussbauteils wie Lastsituationen oder Lagerungen definiert. Darauf aufbauend wird mittels virtueller Produktentwicklung auf Basis von Finite-Element-Analyse (FEA) und Topologie-Optimierung anhand eines iterativen Vorgehens ein kraftflussoptimales Design des Spritzgussbauteils sowie die Position und Gestalt der endlosfaserverstärkten Einleger definiert. Der Fokus bei der Definition der Gestalt der endlosfaserverstärkten Einleger liegt auf der belastungsspezifischen Ausrichtung der einzelnen Endlosfasern im Einleger beziehungsweise dem Spritzgussbauteil unter Berücksichtigung der Fertigungsrestriktionen des Spritzgusses. Hierfür wird anhand von Füllsimulationen ein geeignetes Umschließen der endlosfaserverstärkten Einleger mit dem Kunststoff validiert.
Nach der additiven Fertigung der endlosfaserverstärkten Einleger mittels der Additive-Fusion-Technology (AFT) werden diese in spezifisch gestaltete Aussparungen im Spritzgusswerkzeug eingelegt, um eine exakte Positionierung im Spritzgussbauteil zu gewährleisten. Abschließend erfolgt der Spritzgussprozess, bei dem die endlosfaserverstärkten Einleger gezielt mit dem Kunststoff umspritzt werden. Aufgrund der Kompatibilität des für den Spritzguss verwendeten Kunststoffs und der Kunststoffmatrix der endlosfaserverstärkten Einleger wird eine optimale Verbindung zwischen diesen beiden Komponenten erzielt.
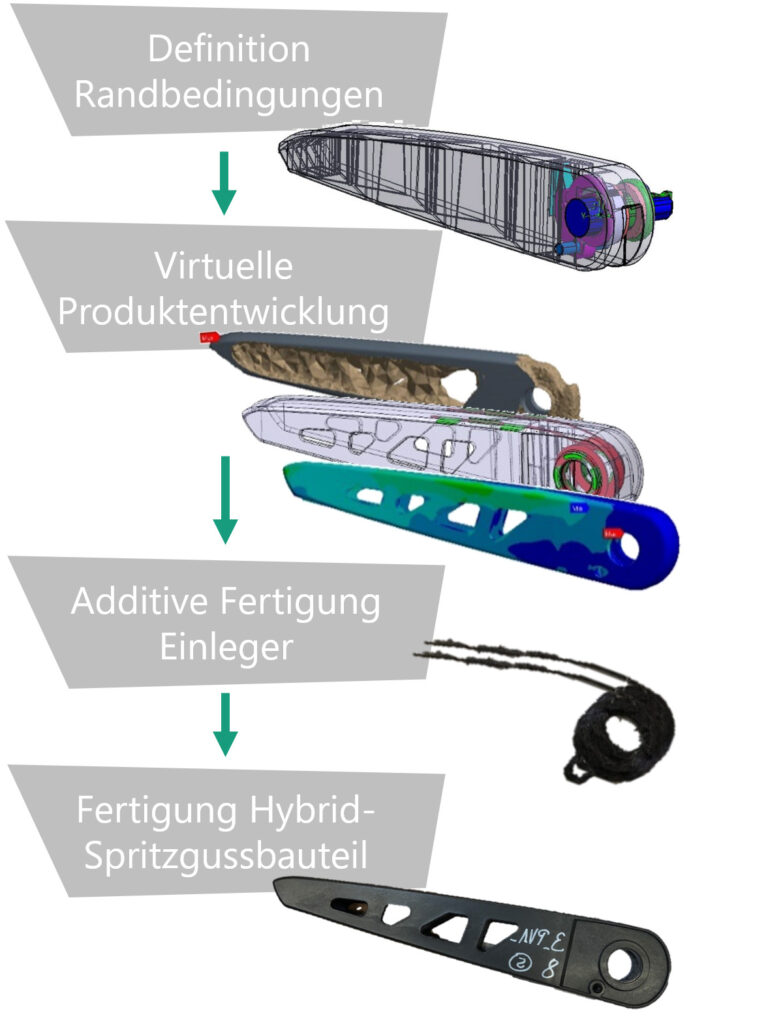
Ergebnis sind leichtere und belastbarere Bauteile
Die im Rahme der Entwicklung des Hybridprozesses ausgelegte und gefertigte Armlehne besitzt unter realen Belastungssituationen, im Vergleich zur konventionell im Spritzguss gefertigten Armlehne, eine um fast 40 Prozent niedrigere Verformung für den kritischen Lastfall bei einer gleichzeitigen Gewichtseinsparung von annähernd 20 Prozent.
Alexander Kalusche, Geschäftsführer der acad group GmbH, sieht daher in dem zum Patent angemeldeten Hybridprozess, der die Vorteile der additiven Fertigung und des Spritzgusses kombiniert, ein großes Potenzial, besonders für eine wirtschaftliche Fertigung von hochbelastbaren Leichtbau-Bauteilen auch in größeren Losgrößen, die bei einer ausschließlich additiven Fertigung nicht möglich ist. Daher möchte Kalusche mit Unterstützung der Projektgruppe Prozessinnovation des Fraunhofer IPA das Hybridverfahren weiter entwickeln und industrialisieren. Hierfür ist die acad group GmbH stets auf der Suche nach Anwendungsfällen aus unterschiedlichsten Branchen wie zum Beispiel Maschinenbau, Automobilindustrie, Luft- und Raumfahrttechnik oder Medizintechnik.
Ihr Ansprechpartner
Jan Felix Kemnitzer
Forschungsteamleiter Additive Prozesse für
innovative Materialien
Telefon: +49 921 78516-412