Quelle: Fraunhofer IPA/Grafik: Emir Cuk
Ohne Band und Takt: Flexibel und produktiv durch die Matrixproduktion
Schneller auf globale Krisen reagieren, mit Lieferengpässen zurechtkommen und gleichzeitig auf individuelle Kundenwünsche reagieren: Matrixproduktionssysteme werden als Lösungsansatz für eine wirtschaftliche Produktion in einem herausfordernden Marktumfeld diskutiert.
Veröffentlicht am 15.06.2023
Lesezeit ca. 9 Minuten
Sie herrscht noch immer in der Industrie vor: Die Linienproduktion mit Fließband und festem Takt. Doch dieses etablierte Produktionssystem stellt Unternehmen immer häufiger vor Herausforderungen. Werden kundenindividuell konfigurierte Produkte oder kürzere Lieferzeiten gewünscht, ändern sich die Prozesse und feste Zyklus- sowie vorgegebene Durchlaufzeiten stimmen nicht mehr. Auch krisen- und umweltbedingte Unterbrechungen der Lieferketten, kurzfristige Stornierungen, Veränderungen der Bestellungen oder der Trend zu immer kleineren Auftragslosen machen die Linienfertigung weniger produktiv und erfordern einen hohen Steuerungsaufwand. Gleichzeitig müssen Unternehmen ihre Produktivität und Resilienz steigern, um im globalen Wettbewerb bestehen zu können.
Bei diesen Anforderungen lohnt es sich, abseits von Band und Takt zu denken, um Flexibilität bei hoher Produktivität zu erhalten. Diesen Lösungsansatz verfolgt die Matrixproduktion, ein flexibles Produktionssystem, das eine Produktion verschiedenster Varianten und skalierbarer Stückzahlbereiche ermöglicht.
Der Begriff Matrix stammt ursprünglich aus der Mathematik und beschreibt eine rechteckige Anordnung von Elementen in Zeilen und Spalten. Produktionstechniker verstehen unter einer Matrix eine schachbrettförmige Anordnung von Produktionsmodulen, die frei verkettet sind. Ein solches Modul kann eine flexible manuelle oder automatisierte Montagezelle oder auch eine stark spezialisierte technologisch geprägte Station sein. Auch Linienabschnitte können als Prozessmodule Teil einer Matrix sein. Ein flexibler Materialfluss – realisiert über einen Logistiker oder eine Flotte fahrerloser Transportsysteme (FTS) – verkettet die frei anfahrbaren Prozessmodule. In hochentwickelten Matrixproduktionen wird dieser Materialfluss cyberphysisch über einen Digitalen Zwilling gesteuert. Durch ihn lassen sich Stoffströme und Maschinenauslastungen optimieren. Mithilfe der Ergebnisse werden dann die realen – physischen – Module gesteuert. Dabei folgt jede Variante ihrem variantenspezifischen Pfad durch das System und Produkte durchlaufen nur die auftragsspezifisch benötigten Prozesse.
Das Produktionssystem wird bereits in Unternehmen unterschiedlicher Branchen umgesetzt. Vorreiter ist die Halbleiter-Industrie, aber auch größere Hersteller im Automotive- und Elektronikbereich setzen modulare Strukturen ein, wie zum Beispiel die Siemens AG im Werk in Karlsruhe.
Dass Matrixproduktionssysteme gerade bei herausfordernden Marktanforderungen eine wirtschaftliche Produktion ermöglichen, zeigt die Veröffentlichung, die das Fraunhofer IPA gemeinsam mit dem Fraunhofer IWU im Auftrag der acatech durchgeführt hat: »Umsetzung von cyber-physischen Matrixproduktionssystemen – Expertise des Forschungsbeirats der Plattform Industrie 4.0«. Thomas Bauernhansl, Institutsleiter des Fraunhofer IPA, ist sich sicher: »Ähnlich wie vor über hundert Jahren das Fließband wird die Matrixproduktion eine neue industrielle Ära einleiten und bald der neue Standard sein.«
Die Umstellung auf ein Matrixproduktionssystem wirft Fragen in unterschiedlichen Produktionsbereichen auf und erfordert interdisziplinäre Expertise.
Modulare Matrixmontage
Wie kann die Montage produktiv und wandlungsfähig gestaltet werden?
Mit der Matrix ergeben sich neue Freiheitsgrade für die Gestaltung, Planung und Steuerung des Montagesystems. Gängige Planungsmethoden im Lean Line Design sind nicht eins zu eins auf die Matrixmontage übertragbar. Bloßes Auseinanderziehen vormals verketteter Stationen und das Auslagern von Sonderausstattungen in Nebenstationen schöpft das Potenzial einer Matrixproduktion bei Weitem nicht aus. Das Fraunhofer IPA hat prozessorientierte Planungsmethoden entwickelt, um Montagesysteme unter Berücksichtigung der spezifischen Rahmenbedingungen als Matrix zu konzipieren und umzuwandeln. Unsere Expertinnen und Experten aus der Gruppe Montageplanung und datengetriebene -optimierung bieten zum Beispiel eine Potenzialanalyse an, gestalten Matrixmontagesysteme und begleiten bei der Transformation. Außerdem führen sie Materialflusssimulationen zum Vergleich von unterschiedlichen Montagestrukturvarianten, wie beispielsweise Linie und Matrix, durch.
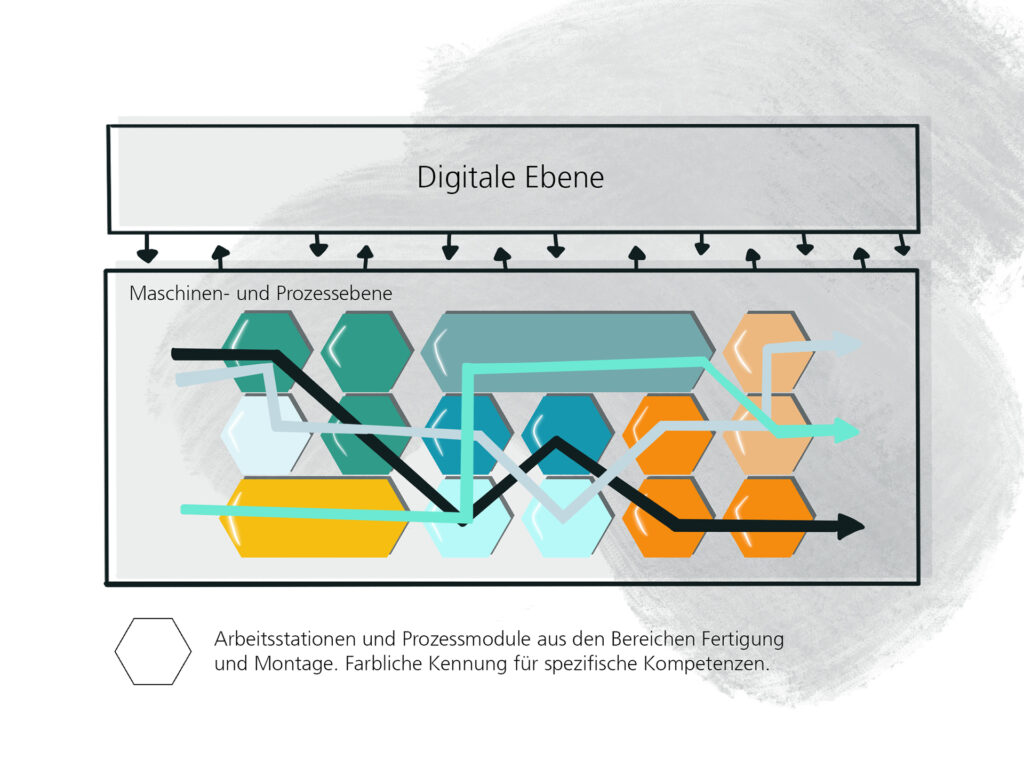
Standardisierte Rekonfiguration
Was muss berücksichtigt werden, wenn das System für neue Herausforderungen umgebaut wird?
Die modulare Struktur von Matrixproduktionssystemen ermöglicht eine hohe Flexibilität für die tägliche Produktion. Je nach Zusammensetzung der Produktionsprogramme oder Integration eines weiteren Produkttyps kann es jedoch sinnvoll sein, die vorhandene Flexibilität anzupassen. In diesem Fall spricht man von Rekonfiguration. In einer Matrixproduktion kann das die Änderung von Funktionsumfängen an Prozessmodulen, die Veränderung der Anzahl von Prozessmodulen oder deren räumliche Neuanordnung sein. Um zu erkennen, wann eine Rekonfiguration sinnvoll ist, wie sie zu gestalten und umzusetzen ist, bedarf es eines standardisierten Prozesses, der in die Organisation der Produktion integriert ist. Diesen Prozess hat das Fraunhofer IPA in sechs Schritte eingeteilt: Von der Prozessplanung und -überwachung über Zielfestlegung, Gestaltung, Ausführungsplanung und Ausführung bis zur Reflexion. Zur Unterstützung des Prozesses bietet sich die Nutzung einer Software an.
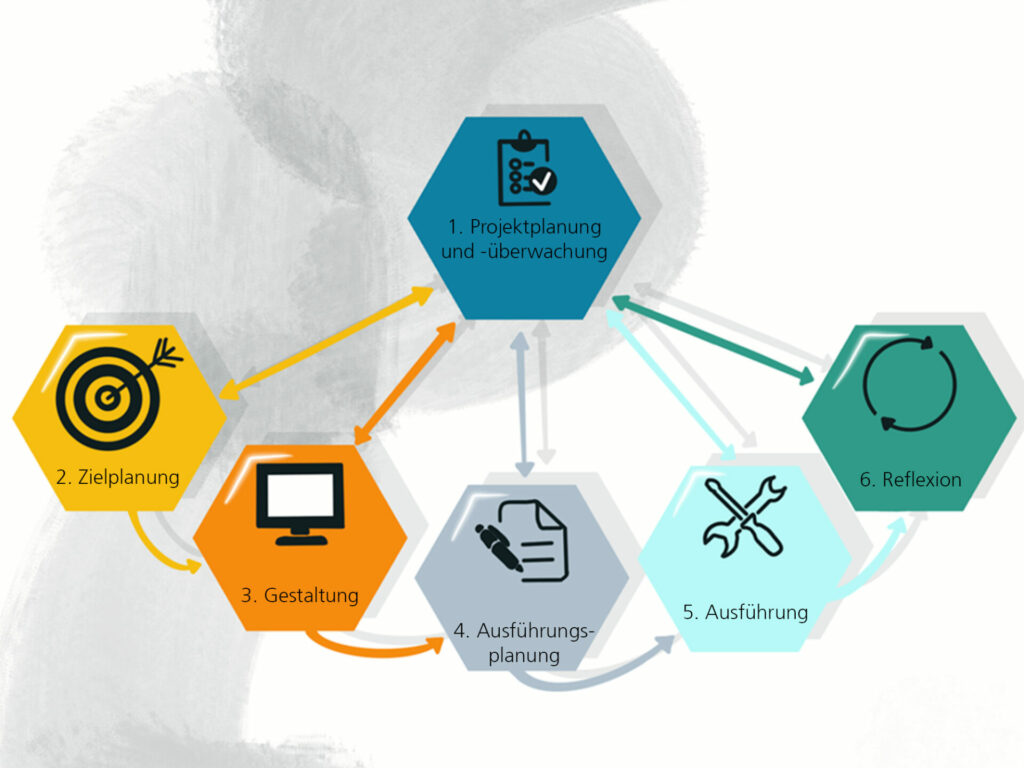
Autonome Auftragssteuerung
Wie können Aufträge optimal durch das System gesteuert werden?
Im Gegensatz zur klassischen Linienproduktion ist der Produkt- und Materialfluss in hochflexiblen Produktionssystemen wie der Matrixproduktion nicht durch das Produktionssystem vorgegeben. Dadurch steigt die Komplexität der Steuerung und unvorhergesehene Ereignisse in der Auftragsabwicklung nehmen zu. Klassische Verfahren der Auftragssteuerung wie Heuristiken sind daher ungeeignet, um diese hochflexiblen Produktionssysteme effizient zu steuern. Selbstlernende Auftragssteuerungssysteme sind in der Lage, diese Lücke zu schließen. Die Gruppe Zuverlässige KI-Systeme am Fraunhofer IPA hat sich daher zum Ziel gesetzt, mit Methoden der Künstlichen Intelligenz Kundenaufträge so zu steuern, dass auf Umweltänderungen in Echtzeit reagiert werden kann und gleichzeitig logistische Zielgrößen wie Produktionskosten, Durchlaufzeit oder Termintreue optimiert werden. Dazu nutzen die Forscher Reinforcement Learning (RL) bei realen Entscheidungsproblemen in der Produktionsplanung und -steuerung. Erste Ergebnisse zeigen, dass mit der RL-basierten Auftragssteuerung für die Matrixproduktion bessere Ergebnisse erzielt werden können als mit gängigen Heuristiken, wie beispielsweise der FIFO-Logik (»first in – first out«).
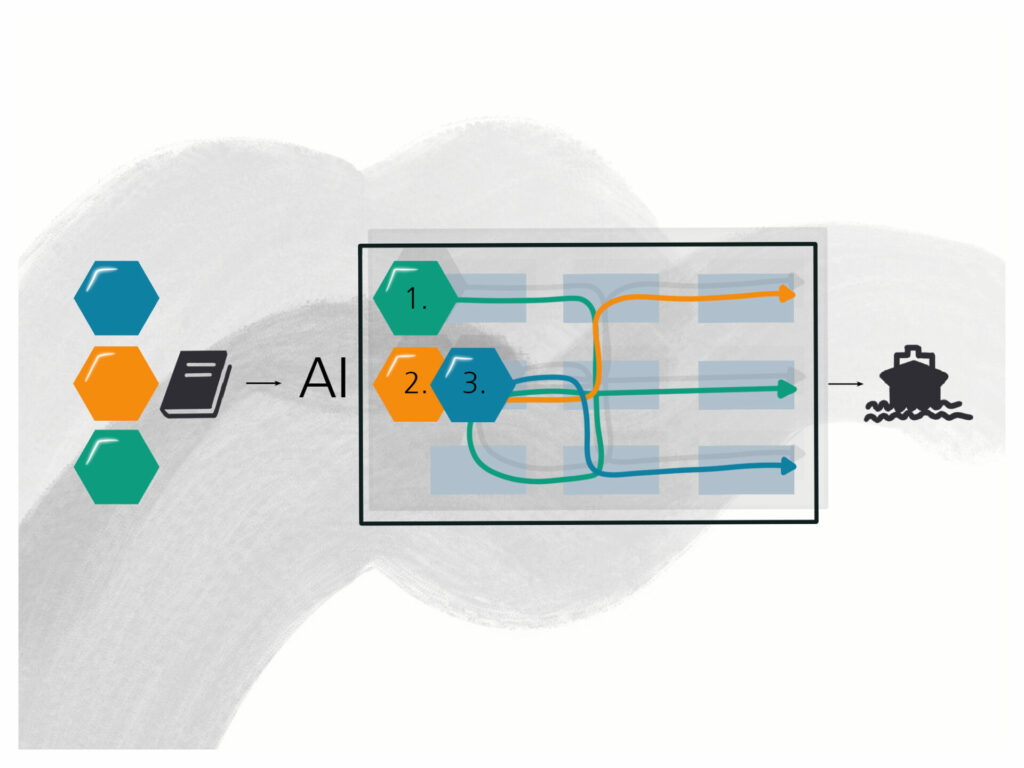
Kostenoptimale Materialbereitstellung
Wie kommt das Material verlässlich und kostengünstig an die Station?
Die Materialbereitstellung macht effiziente Produktionssysteme erst möglich und trägt wesentlich zum Erfolg von Matrixproduktionssystemen bei. Um der hohen Dynamik, unsicheren Nachfragemengen je Station und den Freiheitsgraden zur Auftragsverteilung zu begegnen, entwickelt die Gruppe Montageplanung und datengetriebene -optimierung ein Planungsvorgehen mit der Integration von Simulation und Auswahl-Algorithmen. Dazu wird die geplante Matrixproduktion in einer Simulationsumgebung abgebildet. Mit diesem digitalen Abbild werden im nächsten Schritt Simulationsexperimente durchgeführt, um das dynamische Verhalten zu untersuchen. Aus den in der Simulation bestimmten Verbrauchswerten werden zu erwartende Kosten für alternative Materialbereitstellungsstrategien abgeleitet. Die Informationen zu Verbrauchswerten, Flächenverhältnissen und weitere Angaben werden danach aufgenommen und in eine mathematische Problembeschreibung überführt. Diese soll entsprechend optimal gelöst werden. Dazu haben die Forscherinnen und Forscher unterschiedliche mathematische Lösungswege untersucht und einen geeigneten Algorithmus ausgewählt. Die beiden sequenziell ablaufenden Bausteine »Simulation« und »Auswahlentscheidung« erlauben es, die Planung der Materialbereitstellung kurzzyklisch, automatisiert und parallel zu anderen Tätigkeiten des Planers durchzuführen.
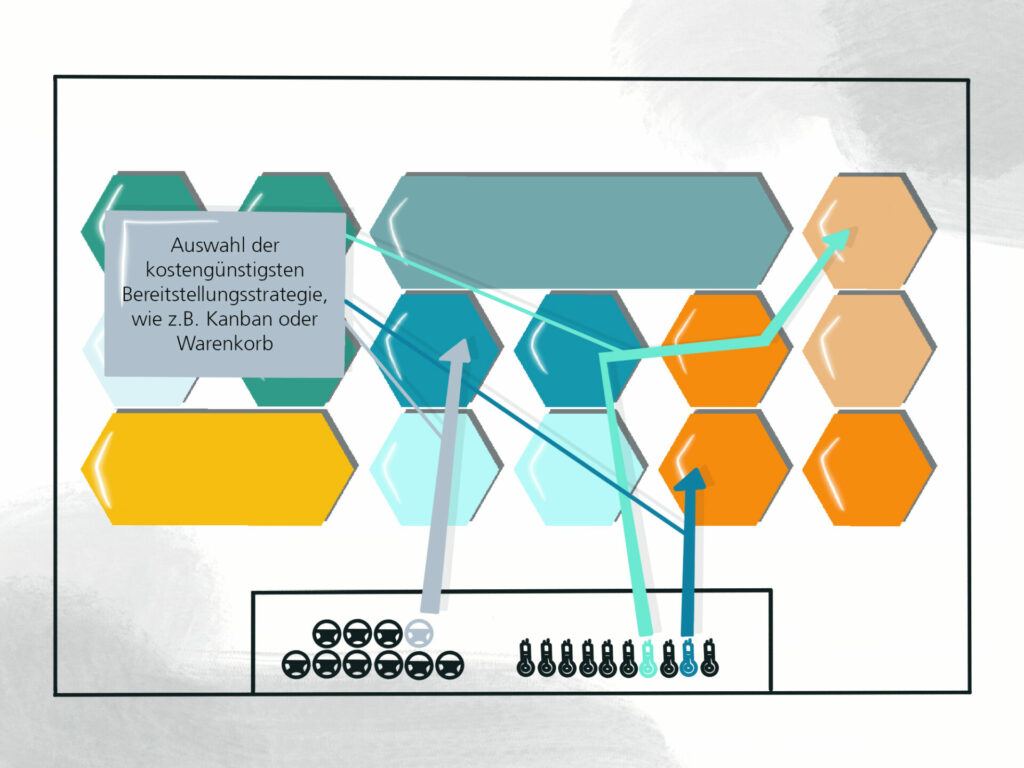
Automatisierte Prozesskontrolle
Wie können Montageprozesse inklusive Füllstände und Prozessfortschritt automatisch erkannt werden?
Um manuelle Montageprozesse in die komplexe Matrixproduktion zu integrieren, werden Systeme benötigt, die automatisiert den Zustand des Prozesses erkennen und an die Steuerung der Matrix zurückgeben können. Damit können abhängige Produktionsschritte in anderen Matrixzellen der aktuellen Situation angepasst werden. Die Schwierigkeit besteht hier darin, unterschiedliche KI-Methoden so zu kombinieren, dass man möglichst flexibel und exakt Informationen aus dem laufenden Prozess extrahieren kann. Um das System ohne großen Aufwand in bestehende Montagezellen integrieren zu können, wird auf einen einzelnen Kamerasensor gesetzt, der den Arbeitsbereich vollständig erfassen kann und sowohl 2D-Farbbilder als auch Tiefenbilder kontinuierlich aufnehmen kann. Auf diese Videodaten werden moderne Bildverarbeitungsalgorithmen angewandt. Die von der Abteilung Bild- und Signalverarbeitung am Fraunhofer IPA entwickelten Methoden zur automatischen Prozesserkennung sind ein wichtiger Bestandteil der komplexen KI-gestützten Matrixproduktion von morgen. Bildverarbeitung ist ein elementarer Bestandteil sowie eine notwendige Schnittstelle zwischen digitaler und realer Welt, um manuelle Prozesse in die automatische Matrixproduktion zu integrieren.
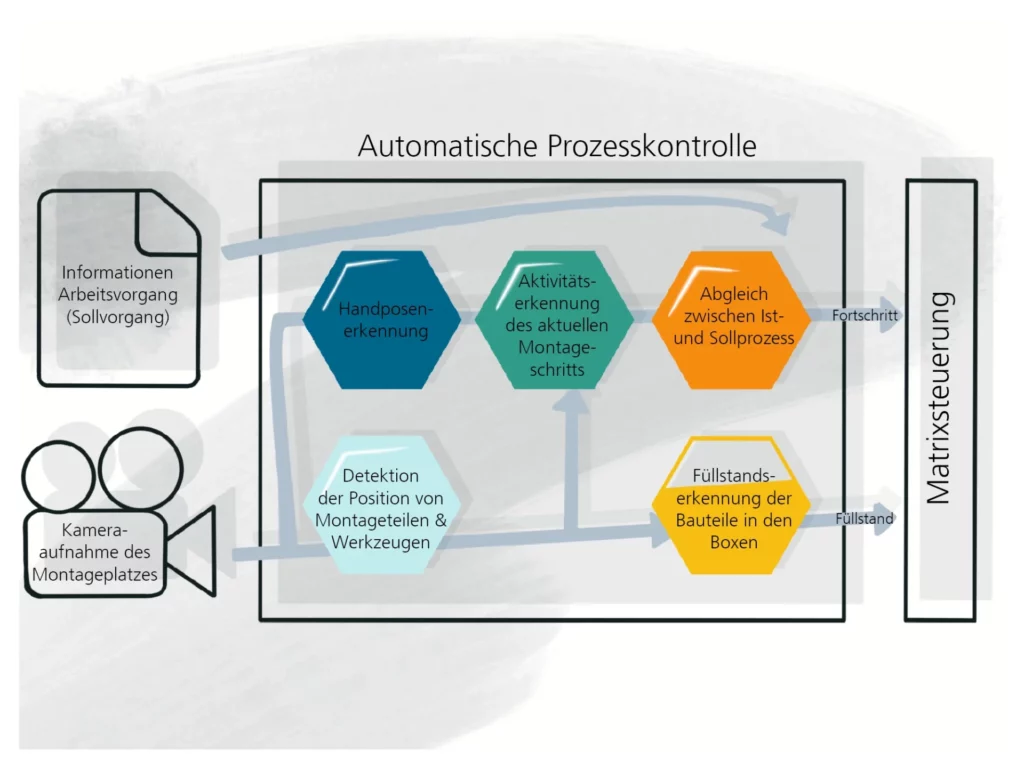
Selbstlernende Roboter
Wie bringen wir Robotern bei, mit der großen Vielfalt an unterschiedlichen Produkten umzugehen?
Der Wunsch nach kundenindividuellen Produkten erfordert lernfähige Roboter in der Produktion, die sich ihre wechselnden Aufgaben selbst beibringen. Die passende Technologie dazu nennt sich Deep Reinforcement Learning und ist ein Teilgebiet der Künstlichen Intelligenz. Dank Simulation übt der Roboter in einer für ihn und den Menschen sicheren, digitalen Umgebung, neue Produkte herzustellen. Dem Roboter wird die Fähigkeit zur sequenziellen Entscheidungsfindung und zum situativen Handeln mit einem längerfristigen Ziel antrainiert. Zudem lernt der Roboter, sicher mit Produktvarianten und sogar Abweichungen in den Produkten oder im Prozess umzugehen, indem diese während des Trainings direkt berücksichtigt werden. Eines der zentralen Ziele der Gruppe Roboterprogrammierung am Fraunhofer IPA ist es also, dem Roboter während des Trainings nicht nur ein Produkt, sondern auch dessen Varianten zu zeigen, damit der Roboter lernt, damit umzugehen, und auch die Produktvariante herstellen kann.
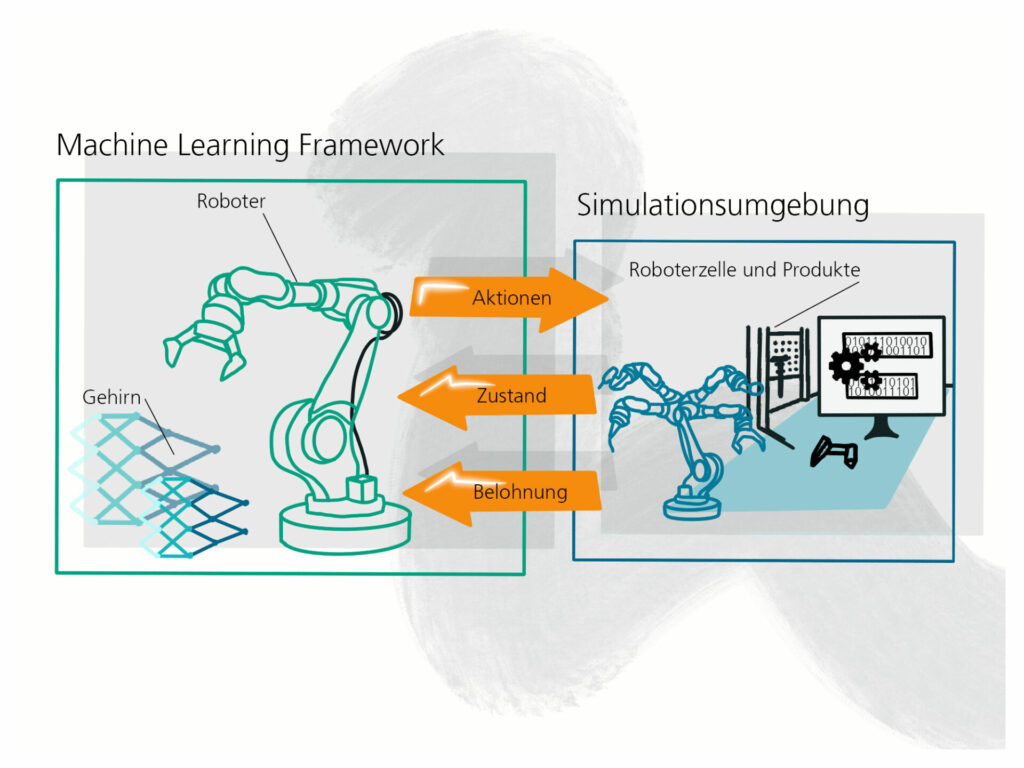
Ihr Ansprechpartner
Gregor Müller
Stv. Leiter des Forschungsteams Montageplanung
Mobil: +49 1520 1051963