Quelle: Festo Vertrieb GmbH & Co. KG
Erfahrungswissen mit Daten kombinieren
Im Rahmen der Lernreise »Fabrik der Zukunft – Lean, Green, Digital«, bei der Bosch und das Fraunhofer IPA Schirmherren sind, ist Festo Best-Practise-Partner. Im Gespräch mit Stefan Schwerdtle, Vice President Corporate Quality, und Sebastian Schill, Senior Vice President Global Production Centre Scharnhausen, erfahren wir mehr darüber, wie Daten erhoben, Menschen befähigt und das Unternehmen mit konkreten Maßnahmen nachhaltiger gestaltet werden kann.
Von den Besten lernen: Das ist nach wie vor das ausgegebene Motto von Georg Wasserloos und seinem Team von macils, das seit vielen Jahren die Lernreisen konzipiert und organisiert. Und egal ob »Lean, Green, Digital« oder »Sicher, Vernetzt, Flexibel«: in Fabriken werden nach wie vor Waren produziert. Nur an der Art und Weise hat sich in den letzten Jahrzehnten einiges verändert. Genau dies gilt es bei den Besuchen der Best-Practise-Partner herauszuarbeiten.
Daten erheben und Fehler beseitigen
So auch bei Festo in Scharnhausen, dem Vorzeigewerk, der Technologiefabrik innerhalb des Gesamtunternehmens. »Wir sind heutzutage deutlich stärker zahlengetrieben als noch vor ein paar Jahren«, erklärt Sebastian Schill, der die Produktion leitet, und führt weiter aus: »Täglich erhalten wir vom Shopfloor aggregierte Zahlen wie Output und Fehlteile, die wir sichten und auswerten können. Das versetzt uns in die Lage, zu sehen, welche Dinge nicht zu 100 Prozent funktionieren – und auch direkt darauf zu reagieren. Das Zauberwort lautet hier Transparenz«.
Weltweit gibt es bei Festo nur ein ERP-System für alle Standorte. Nur so lässt sich Vergleichbarkeit herstellen und mit der Dynamik des Marktes Schritt halten. »Die Geschwindigkeit hat zugenommen. Im Stundenraster kommen neue Aufträge ins Werk«, ergänzt Stefan Schwerdtle, der die Qualität global verantwortet. »Früher waren wir im Halbtagesmodus unterwegs. Mittlerweile sind wir im Rhythmus ‚Hour-by-hour‘ angekommen. An den Maschinen rufen wir die Daten sogar in Echtzeit ab«.
Für Schwerdtle und Schill dienen die Daten hauptsächlich zur Steuerung und Entscheidungsfindung. Wichtige Voraussetzung dabei: Weltweit gibt es eine Referenzorganisation. Das heißt, jedes Werk ist in seinen Strukturen gleich aufgebaut. Berichts- und Kommunikationswege sind in jedem Werk genau gleich. Passend dazu die Analogie zum Auto: Man weiß, in welche Himmelsrichtung man fährt, wie schnell man fährt, wie heiß der Motor ist und vieles mehr. Bezogen auf die Produktion bedeutet das: Abweichungen in der Produktivität lassen sich direkt erkennen. Ein Gegensteuern ist möglich, die Ursachen werden beseitigt und weiter geht’s. Und das im Stundentakt.
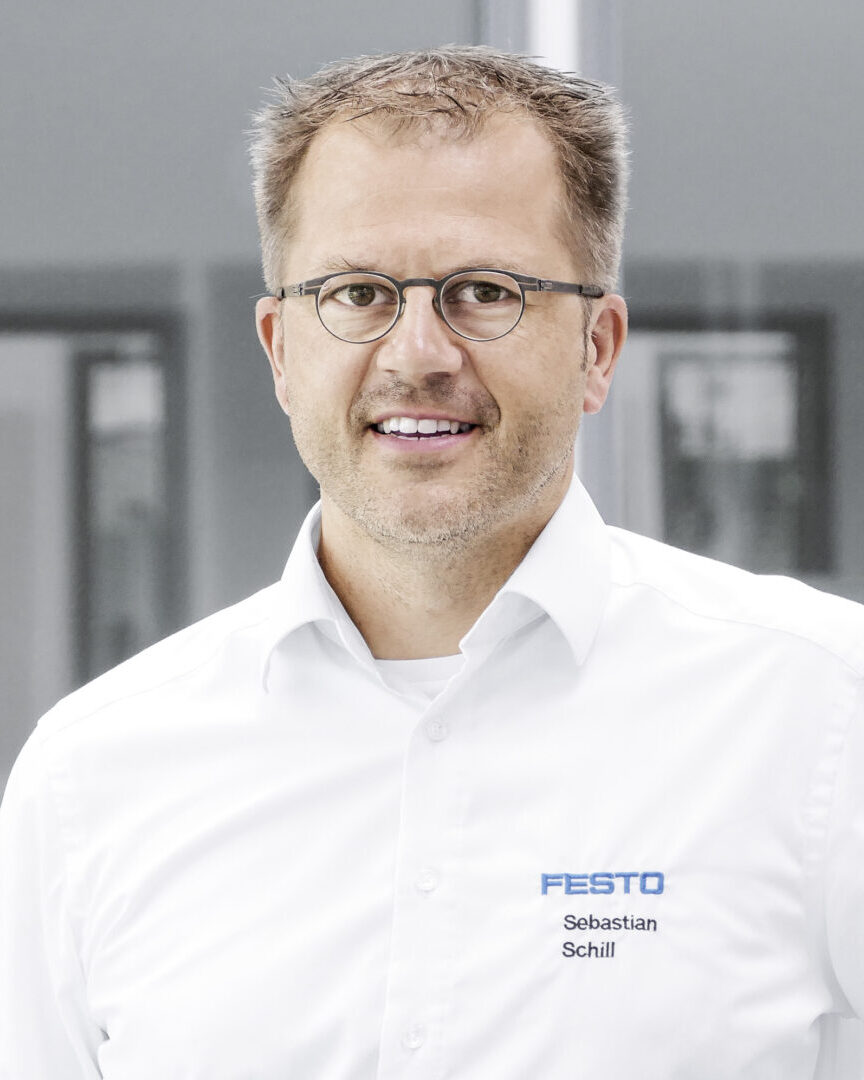
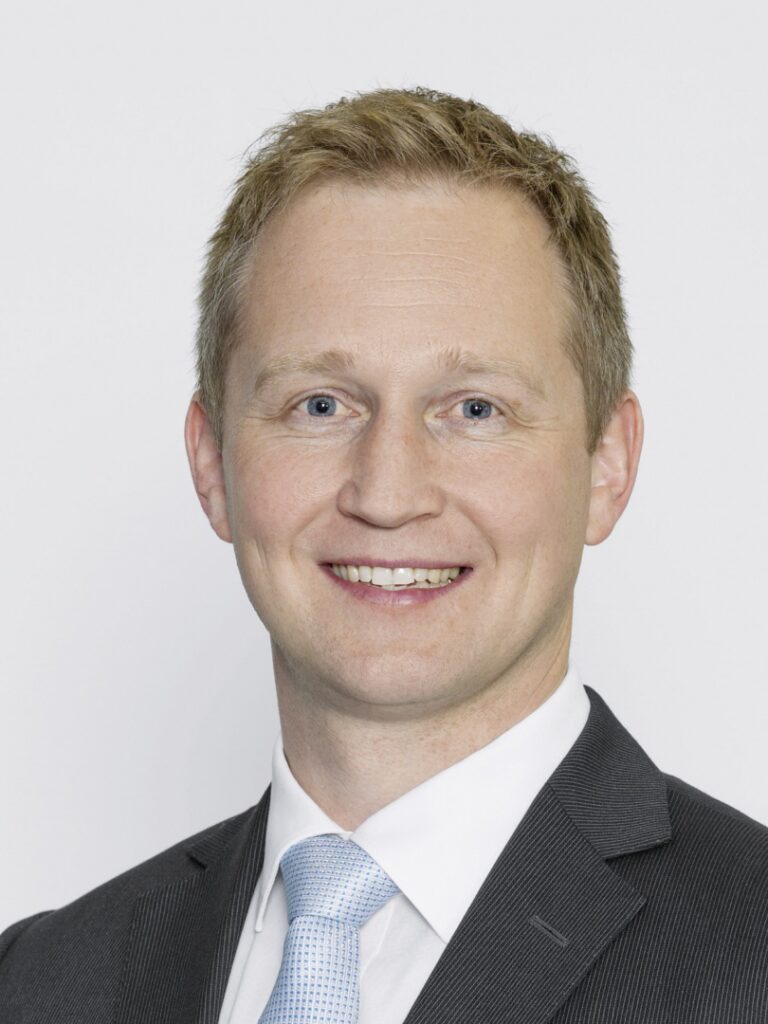
Takt vorgeben und Schritt halten:
Sebastian Schill und Stefan Schwerdtle machen die Produktion im Festo-Werk in Scharnhausen zukunftsfit.
Menschen befähigen und einbinden
Dabei fest im Blick: Quality, Cost, Delivery, das sogenannte QCD-Dreieck. »Am Anfang kamen Mitarbeitende auf mich zu und fragten: Auf was soll ich mich konzentrieren? Die Qualität, die Kosten oder die Lieferung? Meine Antwort: Auf alles. Das ist wirklich die Kunst, aber auch der entscheidende Erfolgsfaktor«, ist Sebastian Schill überzeugt. Stefan Schwerdtle ergänzt: »Die Philosophie des QCD-Dreiecks gilt unternehmensweit. Für alle Bereiche. Auch im Vertrieb. Damit wollen wir ein Stückweit unsere komplexe Welt vereinfachen«. Wenn QCD in Summe passt, hat Festo zufriedene Kunden. Die Herausforderung besteht darin, die Balance zu halten – und die Belegschaft mitzunehmen. Das Stichwort lautet hier Leadership
Konkret auf den Shopfloor runtergebrochen nennen beide ein plakatives Beispiel: den Smart Rework Assistance, eine Eigenkreation der Festo-Mitarbeitenden. Speziell geht es darum, Daten aus dem Produktionsprozess zu nehmen, diese als Muster aufzubereiten und, wenn Nacharbeit am Produkt anfällt, die notwendigen nächsten Schritte systemgestützt vorzuschlagen. Das System gibt also vor, was sinnvoll und richtig ist. Das erleichtert das individuelle Handling und begeistert die Belegschaft. »Die Akzeptanz ist dann am größten, wenn die Mitarbeitenden selbst einen Nutzen haben. Nutzen heißt konkret: Weniger Störung im Arbeitsalltag«, so Sebastian Schill.
Für Stefan Schwerdtle steht fest: »Der Hebel liegt darin, Erfahrungswissen mit Daten zu kombinieren. Und umso mehr Daten und Erfahrungswissen in Kombination vorhanden sind, umso besser funktioniert der gesamte Ablauf«.
Nachhaltig sein und innovativ bleiben
Auch das Thema Nachhaltigkeit ist im Werk in Scharnhausen fest in der DNA verankert. Bereits beim Fabrikneubau im Jahr 2012 war klar: Eine energieeffiziente Fabrik ist ein Muss. Energieeffizienz bedeutet beispielsweise: Die Wärme der Maschinen für Heizungen zu nutzen, alle Beleuchtungen mit LED auszustatten, Controlled Pneumatic zum gesteuerten Luftverbrauch einzuführen und die digitale Schichtplanung mit der Gebäudesteuerung zu koppeln. So ließe sich bis zu 70 Prozent der Energie sparen. Ein bisschen »Smart Home @ Fabrik«, so die Philosophie.
Wir wollen wissen: Nachhaltigkeit und Innovationsfähigkeit – ein Widerspruch oder ein Enabler? Stefan Schwerdtle ist überzeugt: »Ein Enabler, weil es zwingt, größer und breiter zu denken. Innovationen gehen nicht eindimensional«. Mächtiges Kapitel im Standard-Lastenheft der Anlagenbeschaffung sei neben der IT-Security auch das Thema Energieeffizienz. »Innovation heißt für mich auch Schlichtheit. Mit einer Einfachheit zu einer Lösung kommen. Da kommen wir langsam hin. Ich gebe Ihnen ein Beispiel: Wir haben uns einen 3D-Drucker angeschafft, um kleine Bauteile vor Ort zu drucken, schnell einzuspielen und auszuprobieren. Das schafft Freiräume für die Mitarbeitenden«, setzt Sebastian Schill noch einen drauf.
Und was braucht Deutschland als Produktionsstandort, um langfristig wettbewerbsfähig zu bleiben? Flexibilität, um flexibel auf die Volatilität des Marktes reagieren zu können. Denn an Können, Wissen und Mut, neue Dinge anzugehen, fehlt es nicht. Ingenieurskunst ist das Fundament für den Wohlstand. Aber die Rahmenbedingungen müssen passen, da sind sich beide Festo-Mitarbeiter einig. Abschließend möchten wir noch wissen, wie man nach so viel lean, green und digital am besten entspannen kann. Die Antwort: Raus in die Natur auf die Schwäbische Alb mit Kind und Kegel, ab und zu Fußball spielen oder am Traktor oder Oldtimer rumschrauben. Schwäbisch bodenständig – oder einfach nur gut.
Industrie trifft Forschung:
Interdisziplinäre Zusammenarbeit auf breiter Basis
Von der Natur inspiriert: In Anlehnung an den Rüssel eines Elefanten und unter Einsatz generativer Fertigungstechnologien konstruierte Festo in Zusammenarbeit mit dem Fraunhofer IPA einen bionischen Handhabungsassistenten. Für diesen Hightech-Helfer für Industrie und Haushalt gab es 2010 den Deutschen Zukunftspreis – überreicht vom damaligen Bundespräsidenten Christian Wulff.
Im Jahr 2022 führte Festo im KI-Fortschrittszentrum »Lernende Systeme und Kognitive Robotik«, das Teil des Cyber Valley ist und von den Fraunhofer-Instituten IAO und IPA geführt wird, einen Quick-Check von MRK-Applikationen (Mensch-Roboter-Kollaboration) durch. Evaluiert wurde die digitale Planungstoolchain.
Im interdisziplinären Austausch steht Festo mit dem Fraunhofer IPA im Forschungsprojekt »InterOpera – Digitale Interoperabilität in kollaborativen Wertschöpfungsnetzwerken der Industrie 4.0«. In dem vom Bundesministerium für Wirtschaft und Energie geförderten Projekt sollen einheitliche Standards für die Industrie 4.0 erarbeitet werden.
Weitere Anknüpfungspunkte: Austausch und
Zusammenarbeit
– im EU-Projekt »Futuring«, das eine Zukunftsvision und Handlungsempfehlungen für die produzierende Industrie in Europe erarbeitet,
– bei der Plattform Biointelligente Produktion (BIM), einem Teilbereich von ManuFUTURE, zur Erschließung und Etablierung biointelligenter Fertigung
– sowie in der Vorbereitung eines Leuchtturmprojekts für die »Manufacturing-X«-Initiative der Plattform Industrie 4.0 zur Digitalisierung der Lieferketten in der Industrie.
Nächste Lernreise startet im September 2023
Von den Besten lernen heißt auch: Immer in Bewegung bleiben und Neues erfahren. Daher geht die Lernreise in die nächste Runde. Das Motto diesmal: »Produktion der Zukunft – Die resiliente Fabrik. Sicher, vernetzt, flexibel«. Schirmherr ist neben dem Fraunhofer IPA, repräsentiert durch Institutsleiter Prof. Thomas Bauernhansl, auch Siemens. Das Werk in Karlsruhe macht am 13./14. September direkt den Auftakt.
Mehr zur Lernreise:
https://www.share2perform.com/lernreise/produktion-der-zukunft
Ihre Ansprechpartnerin
Anja Demont
Leiterin Business Development
Telefon: +49 711 970-1076