Weniger Umweltbelastungen in der Lackiertechnik
Durch richtiges Prüfen und gezielte Optimierungen lassen sich die Emissionen in der Lackiertechnik mindern. Gemeinsam mit einem Unternehmen hat das Fraunhofer IPA die wiederkehrenden Messungen der Staubemissionen durchgeführt.
Veröffentlicht am 15.07.2021
Lesezeit ca. 4 Minuten
Im Maschinen- und Anlagenbau werden viele Produkte mit Lacken beschichtet, die organische Lösemittel enthalten. Durch weitere eingesetzte Betriebsstoffe wie Reiniger oder Verdünner kommen weitere Lösemittelemissionen hinzu. Unabhängig von der Genehmigungspflicht ist es sowohl bei bestehenden als auch bei den neu geplanten Anlagen erforderlich, die Nachweise über die Verbräuche durch geeignete Messungen an die Behörden zu übermitteln. Da die Überwachung kontinuierlich erfolgen kann, ist eine Alternative hierzu die Überprüfung durch wiederkehrende Messungen. Die Anforderungen für die Anlagen ergeben sich aus der 31. Bundesimmissionsschutz-Verordnung (BImschV) und aus der Technischen Anleitung zur Reinhaltung der Luft (TA Luft).
Gemeinsam mit einem Unternehmen mit etwa 40 000 Mitarbeitern hat das Fraunhofer IPA die wiederkehrenden Messungen der Staubemissionen durchgeführt, die im Folgenden beschrieben werden.
Messverfahren und Messung
Um die Messungen von Partikeln in der Abluft durchzuführen, hat ein Forschungsteam des Fraunhofer IPA ein Messgerät im Einsatz, das die Staubbeladung gravimetrisch bestimmt (nach DIN EN 13284-1 beziehungsweise VDI 2066 Blatt I). Die Gravimetrie ist ein quantitatives Analyseverfahren, bei dem die Messung von Stoffmengen auf der Bestimmung der Masse beruht. Dabei dienen Glasfaserfilter als Probekörper. Diese werden vor der Messung konditioniert und ausgewogen, um ein Referenzgewicht zu erhalten. Die Filter werden dann in eine Entnahmesonde platziert. Die Sonde mit dem Filter wird nach dem Prinzip der In-Stack-Filtration an den repräsentativen Messstellen des Abluftrohrs in den Abgasstrom eingebracht und der Teilvolumenstrom entnommen. Die Entnahme erfolgt isokinetisch, also geschwindigkeitsgleich in Bezug auf die Abluftgeschwindigkeit.
Die Messstelle ist so zu wählen, dass dort ein ausreichend stabiles, also homogenes Geschwindigkeitsprofil vorherrscht. Im Idealfall beträgt die Ein- und Auslaufstrecke den fünffachen Durchmesser des Abgaskanals.
Hintergrund
Nach Industrieemissionsrichtlinie 2010/75/EU ist der Betrieb der Anlage genehmigungspflichtig, wenn 200 t/a oder 150 kg/h und mehr Lösemittel verbraucht werden. Für Deutschland gilt speziell die 4. Bundesimmissionsschutz-Verordnung, abgekürzt BImschV. Diese schreibt daneben ein vereinfachtes Genehmigungsverfahren ab einem Schwellenwert von 25 kg/h bis 150 kg/h oder ab 15 t/a bis 200 t/a vor.
Nach der TA Luft beträgt der Grenzwert der staubförmigen Emission im Abgas (Lackpartikel) für Anlagen zur Behandlung von Oberflächen für den Massenstrom 15 g/h oder für die Massenkonzentration 3 mg/m³. Wenn dieser Wert überschritten wird, so müssen luftreinigende Maßnahmen, wie etwa weitere Filterstufen, eingesetzt werden.
Bei neu errichteten Anlagen und bei Anlagen, die einer wesentlichen baulichen oder technischen Änderung unterliegen, erfolgen Messungen frühestens drei Monate und spätestens sechs Monate nach der Inbetriebnahme, danach sind Messungen bei bestehenden Anlagen im Turnus von drei Jahren wiederkehrend auszuführen. Die Messprotokolle werden den zuständigen Behörden vorgelegt.
Zur Berechnung der isokinetischen Absaugrate sowie der tatsächlichen Dichte des Rauchgases müssen im Vorfeld der Messung Druck und Temperatur des Abgases gemessen werden. Bezugswerte sind dabei nach VDI 2066-1 der Standard-Atmosphärendruck (101,3 kPa) und der absolute Nullpunkt (273,15 K).
Die bei der anschließenden Messung entnommene Abluft wird durch den Filterkörper geleitet. Die darin enthaltenen Staubpartikel werden auf dem Filter abgeschieden. Aus dem Gewichtunterschied lassen sich dabei Rückschlüsse auf die Staubbeladung der Abluft ziehen.
Nach der Berechnung der Rauchgasdichte kann die Abgasgeschwindigkeit ermittelt und mit den Werten des Messgeräts validiert werden. Nach der Validierung erfolgt die Berechnung des abgesaugten Volumens. Dieses kann auch mit Hilfe eines Zählers zur Referenz aufgenommen werden. Für einen Bezug der Staubkonzentration auf trockenes Abgas muss zudem der Feuchtegehalt des Abgases gemessen werden.
Neben der Staubpartikelmasse werden auch weitere relevante Parameter aufgenommen. Diese sind unter anderem der statische und dynamische Druck sowie Temperatur und Feuchtigkeit des Abgases.
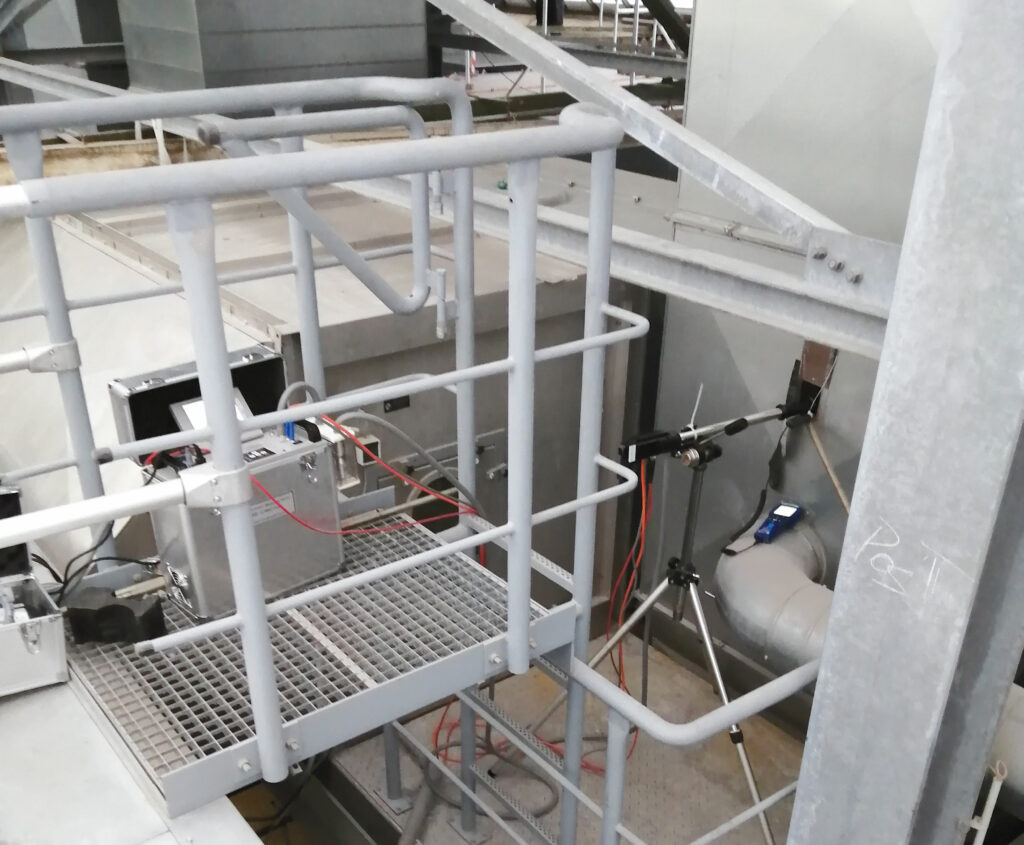
Auswertung
Nach der Berechnung der Rauchgasdichte kann die Abgasgeschwindigkeit ermittelt und mit den Werten des Messgeräts validiert werden. Nach der Validierung erfolgt die Berechnung des abgesaugten Volumens. Dieses kann auch mit Hilfe eines Zählers zur Referenz aufgenommen werden. Für einen Bezug der Staubkonzentration auf trockenes Abgas muss zudem der Feuchtegehalt des Abgases gemessen werden.
Aus dem während einer angemessenen Messdauer abgesaugten Volumenstrom, der durch Differenzwägung ermittelten Staubmenge und den im Vorfeld gemessenen Druck-Temperatur- und Feuchtewerte lässt sich schließlich die Staubbeladung des Abgases in mg/m3 berechnen.
Ergebnis
Liegt die ermittelte Staubkonzentration in der Anlage an jeder Messstelle unter dem maximal zulässigen Grenzwert von 3mg/m³, so ist ein sicherer Betrieb gewährleistet und es sind seitens Betreiber keine weiteren Maßnahmen zur Minimierung der Staubemission notwendig. Sollte die Einhaltung der vorgeschriebenen Grenzwerte unsicher sein, können Maßnahmen durch das Fraunhofer IPA geplant werden.
Ihre Ansprechpartner
Volker Wegmann
Geschäftssegmentleiter Oberflächen
Telefon: +49 711 970-1753
Michael Nazar Bogdan
Mitarbeiter des Forschungsteams Prüftechnik und Lackierprozessentwicklung Beschichtungen
Telefon: +49 711 970-1090
Wolfgang Niemeier
Mitarbeiter des Forschungsteams Spritzlackierung und Simulationen
Telefon: +49 711 970-1791