Quelle: Fraunhofer IPA/Foto: Rainer Bez
Der Griff-in-die-Kiste
Ein Beispiel für eine taktgebende Technologie ist der Griff-in-die-Kiste. Seine Entwicklung zeigt exemplarisch den Weg vom Forschungsergebnis zum kaufbaren Produkt bei der Liebherr-Verzahntechnik GmbH. Die Technologie wird unter dem Motto »Automation for Automation« bis heute weiterentwickelt.
Ein Roboter fährt seinen Arm über eine Gitterbox mit Schüttgut, verharrt kaum einen Moment, greift hinein, hebt ein Teil heraus, legt es ab, um gleich wieder in dem Haufen chaotisch gelagerter Werkstücke zu verschwinden, Guss-, Stanz- oder Schmiedeteile aus der Kiste zu vereinzeln und in korrekter Lage und Orientierung zur Weiterbearbeitung in einen Werkstückträger einzulegen – bis die Gitterbox leer ist. Hinter dieser so leicht und mühelos erscheinenden Anwendung steckt jahrzehntelange Forschungsarbeit: der Griff-in-die-Kiste.
Das Fraunhofer IPA erarbeitet hierfür bereits seit vielen Jahren Technologien. So meldete das Institut bereits 2007 seine Objekterkennungsverfahren zum Patent an und zeigte eine damit umgesetzte Anwendung ein Jahr später auf der Automatica. Während Griff-in-die-Kiste-Zellen heute verbreitete Exponate sind und auch in Produktionen Einzug halten, war die Roboterzelle des IPA zu dem Zeitpunkt noch eine Seltenheit. Zur gleichen Zeit hatte das Forscherteam um den Griff-in-die-Kiste erstmals Kontakt mit der Firma Liebherr-Verzahntechnik.
Als Werner Kraus, heutiger Leiter der Abteilung Roboter- und Assistenzsysteme, 2009 mit dem Griff-in-die-Kiste in Berührung kam, sah es wirtschaftlich in Deutschland und der Welt düster aus. Die Finanzkrise hatte deutliche Spuren hinterlassen und der ifo-Geschäftsklimaindex einen Tiefpunkt erreicht. Damals steckten die Technologien für den Griff-in-die-Kiste, vornehmlich effiziente Objekterkennungsverfahren, noch in den Kinderschuhen. Existierende Lösungen wie Vibrationswendelförderer waren nicht ausreichend flexibel.
Oft übernahm deshalb ein Mitarbeiter das Vereinzeln. Dies geschah unmittelbar an der Produktionslinie, war monoton, dreckig und körperlich belastend wegen der hohen Gewichte der Werkstücke und der nicht ergonomischen Haltung beim Greifen aus der Kiste. Eine typische »3D-Aufgabe«: dull, dirty, dangerous. Diese Belastung für die Mitarbeiter und eine übliche Amortisation von weniger als zwei Jahren im Dreischicht betrieb motiviert sowohl die Beschäftigten als auch das Manage-ment, einen roboterbasierten Griff-in-die-Kiste einzusetzen.
Intensive Zusammenarbeit führt zur ersten industriellen Umsetzung
»Weil es eine wirtschaftlich schwierige Zeit war, plante Liebherr, sich strategisch neu auszurichten«, erklärt Kraus. »Sie wünschten, nicht mehr ›nur‹ Maschinenhersteller zu sein, sondern wollten sich zum Gesamtlösungsanbieter wandeln, nicht mehr ›nur‹ Verzahnmaschinen verkaufen, sondern eine gesamte Fertigungszelle.« Darin sollte ein Roboter die Bauteile der Maschine anreichen und sie nach der Bearbeitung dem nächsten Schritt im Prozess zuführen. »Die jahrelange Zusammenarbeit zwischen Liebherr und IPA hat sich ausgezahlt, und das begeistert mich«, blickt Kraus zurück. Gemeinsam gingen das IPA und Liebherr durch schwierigere und erfolgreichere Zeiten und erarbeiteten Meilensteine: 2010 gab es den ersten »Proof of Concept« einer Roboterzelle, die die Bauteile handhaben konnte. Ein Jahr später folgte die erste Realisierung für semichaotisch, 2013 für vollständig chaotisch gelagerte Bauteile.
Skalierungsherausforderung
Zu dem Zeitpunkt waren alle Beteiligten euphorisch und glaubten, der Technologietransfer in die Industrie sei gelungen. Die Auszeichnung mit dem »handling«-Award bestätigte dies zunächst. Aber – einmal »gemacht« genügt nicht. Kraus: »Als es darum ging, die erarbeitete Lösung zu skalieren, mussten wir noch einige Hürden nehmen. Wir wollten den Griff-in-die-Kiste in einem anderen Projekt einsetzen, um Pleuel auf den Werkstückträger zur anschließenden spanenden Bearbeitung zu legen. Aber die Geschwindigkeit stimmte nicht. Wir sind drangeblieben, haben für die Abnahme der Zelle gekämpft und dies letztlich auch geschafft.« Die gewonnenen Kenntnisse konnten die IPA-Forscher für die Liebherr-Anwendung nutzen und diese weiter verbessern. Außerdem haben sie eine graphische Bedienoberfläche entwickelt, um die Software nutzerfreundlicher zu machen.
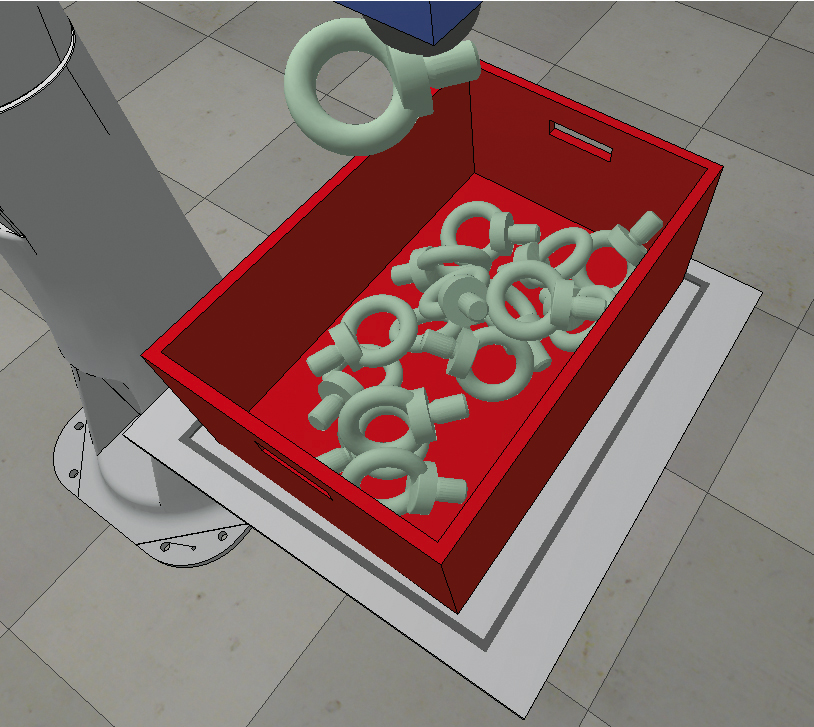
Best-of-Industry-Award
2017 gewann Liebherr mit seiner Gesamtlösung rund um die Griff-in-die-Kiste-Technologie des Fraunhofer IPA den »Best-of-Industry«-Award. Und seit vergangenem Jahr ist die Technologie in deren Produktportfolio auch für weitere Roboterintegratoren als Technologiepaket »LHRobotics.Vision« verfügbar. IPA und Liebherr profitieren gleichermaßen vom Wissenstransfer. »Technologien kundenspezifisch entwickeln, stets verbessern und nachfassen, Hürden systematisch überwinden und gemeinsam den Weg bis zum Ziel gehen.« So formuliert Kraus das Innovationsverständnis.
Griff-in-die-Kiste hinter den Erwartungen
Liebherr machte damals in Krisenzeiten den richtigen Schritt und stellte Weichen für die Zukunft. Und auch das IPA arbeitet schon seit ein paar Jahren am Griff-in-die-Kiste der Zukunft: mehr Autonomie, bessere Taktzeiten, größere Robustheit dank Verfahren des Maschinellen Lernens. Denn kritisch betrachtet, liegt die Verbreitung des Griff-in-die-Kiste noch weit hinter den Erwartungen zurück. Jährlich werden weltweit über 200.000 neue Roboter für die Handhabung installiert. Von diesen führt ein Anteil im Promillebereich den Griff-in-die-Kiste aus. Das Gros der Roboter dagegen greift blind oder nutzt maximal eine 2D-Bildverarbeitung für semichaotische Anlieferung wie beispielsweise beim Depalletieren.
Gleichzeitig finden sich in Produktionen unzählige Vereinzelungsschritte, die per se für den Griff-in-die-Kiste geeignet wären, ganz zu schweigen von Anwendungspotenzialen in der Logistik. Das seit Jahrzehnten bestehende Anwenderproblem der eingangs genannten »3D-Aufgaben« ist trotz guter Wirtschaftlichkeit also auch heute noch sehr groß und nicht gelöst.
Ein Grund hierfür: Zellen mit dem Griff-in-die-Kiste sind das erste Glied einer verketteten Produktions- oder Montagelinie. Die Austaktung solch einer verketteten Linie basiert darauf, dass jede Station eine garantierte Leistung erbringt. Der »typische« Griff-in-die-Kiste bringt hier zwei Unsicherheiten mit: »Noch immer ist nicht garantiert, dass ein Roboter alle Teile aus der Kiste entnehmen kann. Die letzten verbleibenden Teile müssen dann händisch vereinzelt werden«, beschreibt Kraus das Problem. Weiterhin steigt mit zunehmender Kistenentleerung auch die Taktzeit deutlich an. »Die Schwankungen in der Taktzeit können entweder über Worst-Case-Auslegung oder Puffer ausgeglichen werden. Die ganze Linie passt sich also einer möglicherweise hohen Taktzeit an oder der Griff-in-die-Kiste startet früher und erarbeitet sich einen »Vorsprung«, um Stillstände zu verhindern«, so Kraus. »Diese Unsicherheiten verhindern aktuell den breiten Einsatz des Griff-in-die-Kiste in der Praxis.«
»Vision Zero«: vollständige Kistenleerung bei gleichbleibender Taktzeit
Diese zentralen Probleme geht das Fraunhofer IPA mit seiner »Vision Zero« an, dem Ziel, die Kiste bei gleicher Taktzeit vollständig zu leeren. Die Gründe, warum die Vision heute noch nicht Realität ist, sind vielfältig: »Es kann an der Bildverarbeitung liegen, an ungeeigneten Sensoren oder Greifern, verbunden mit schwierig zu greifenden Objekten oder sonstigen kundenspezifischen Herausforderungen«, erklärt Kraus. »In Summe haben wir acht typische Endanwenderprobleme identifiziert, die den Einsatz des Griff-in-die-Kiste limitieren. Hierfür entwickeln wir Lösungsansätze und greifen zum Teil auf neue Technologien wie das Maschinelle Lernen zurück.«
Die Praxis zeigt beispielsweise, dass der Entleerungsgrad und die Taktzeiten aktuell sehr stark von der Expertise des Einrichters abhängen. Die IPA-Forscher arbeiten daher an Algorithmen zur Selbstkonfiguration des Griff-in-die-Kiste-Systems, die automatisch die Parameter auf dem Niveau eines Experten einstellen. Das betrifft unter anderem die Hand-Kamera-Kalibrierung, die Parametrierung der Algorithmen oder die Greifpunktgenerierung.
Der Greifer als Schlüsselkomponente
Das Greiferdesign ist die Grundlage für eine vollständige Kistenentleerung. Denn einerseits bedingt es die Anzahl der möglichen Greifpunkte am Werkstück und somit die Flexibilität der Anwendung, andererseits trägt es mit seiner Kontur als Ganzes zum erfolgreichen Ablauf bei, beispielsweise durch seine Anfälligkeit für Kollisionen. In der Praxis wird dieses wichtige Element oft nach »Bauchgefühl« ausgewählt und die Leistung erst während der Inbetriebnahme des Robotersystems ersichtlich. »Um hier zu einer begründeten Auswahl zu gelangen, setzen wir eine Simulationsumgebung zur Verifikation des Greiferdesigns ein«, hebt Kraus hervor. Darin werden 3D-Punktewolken von virtuell gefüllten Kisten erzeugt und anhand derer Aspekte die Zugänglichkeit des Greifers zum Werkstück ohne Kollision statistisch evaluiert. Ohne Hardware-Investitionen und Tests an der realen Produktion, die dafür stillstehen müsste, können somit vielfältige Greiferdesigns durchgespielt und deren Leistungsfähigkeit nachgewiesen werden. Liebherr entwickelt das Simulationstool im Austausch mit dem IPA entsprechend den Industriebedarfen weiter, sodass es einfacher und produktiver verwendet werden kann.
Neues Niveau durch Maschinelles Lernen
Ein weiterer Grund, warum die Taktzeiten bei fast leeren Kisten steigen bzw. der Roboter die Kisten nicht vollständig leeren kann, ist die Herausforderung für die Objekterkennung, die Teile am Kistenboden korrekt zu erkennen. Kraus beschreibt die Schwierigkeiten zum Beispiel bei Blechteilen: »Die Teile sind glänzend, dünn und schlecht zu erkennen, weil sie in der 3D-Punktewolke mit dem Kistenboden verschmelzen.« Um die Kiste dennoch leer zu bekommen, nutzen die Forscher ein tiefes neuronales Netz zur Segmentierung. Anschaulich gesprochen, schneidet das neuronale Netz die Bereiche der Punktewolke mit Werkstücken aus, segmentiert diese also, und übergibt die Segmente an die weitere Bildverarbeitung. Durch die Vorverarbeitung werden auch die letzten Teile in der Kiste zügig und zuverlässig erkannt.
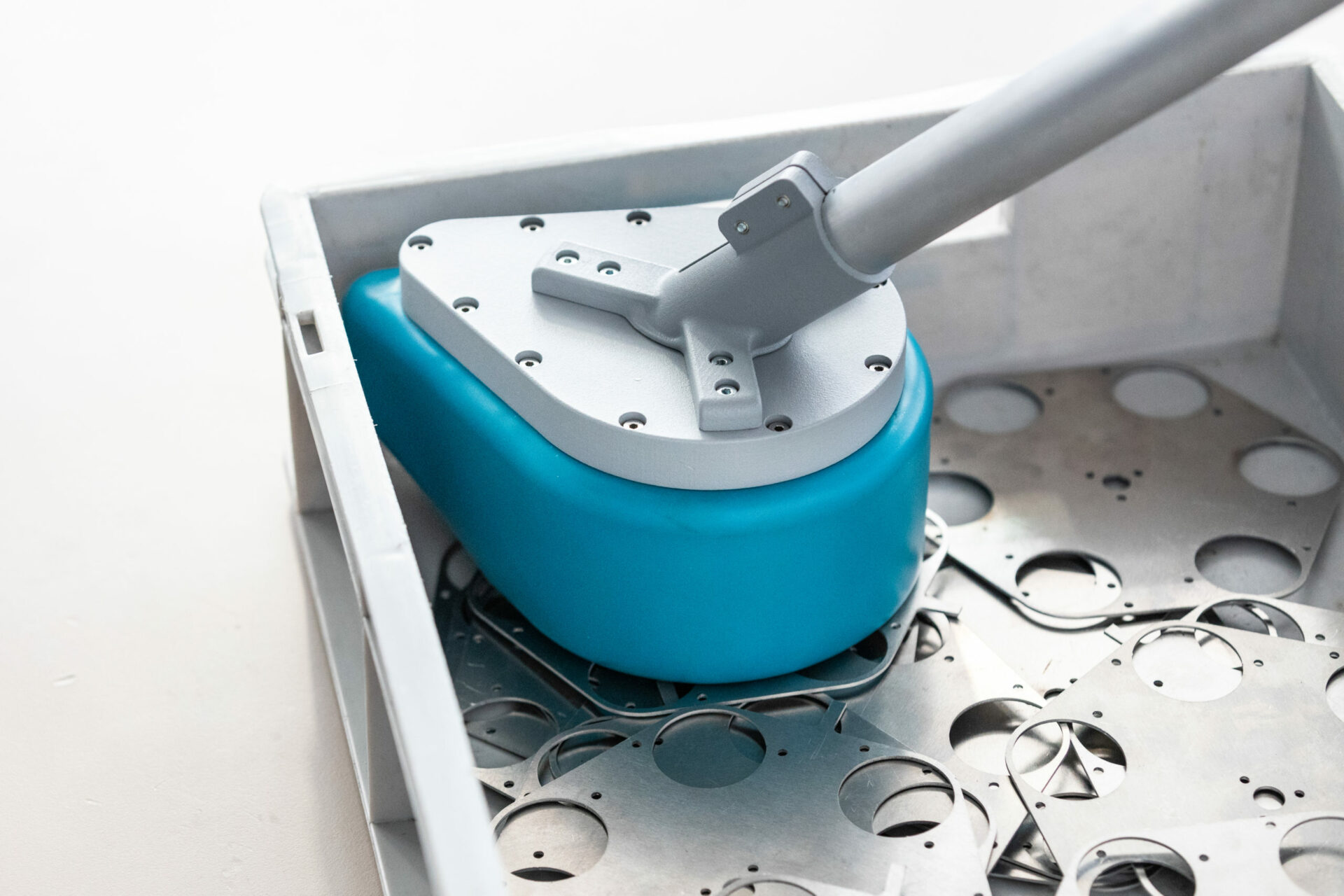
Automatisierung der Automatisierung
Das Fraunhofer IPA fasst die neuesten Entwicklungen unter dem Motto »Automatisierung der Automatisierung« zusammen. Damit ist gemeint, dass künftig zum Beispiel die Planung von Automatisierungslösungen autonomer ablaufen soll oder dass sich Produktionsmittel wie Roboter automatisch rekonfigurieren, wenn eine neue Produktvariante gefertigt wird. Die oben beschriebenen Eigenschaften der IPA-Lösungen für den Griff-in-die-Kiste zeigen, wie eine solche »Automatisierung der Automatisierung« möglich wird.
Unternehmen können Griff-in-die-Kiste-Software erproben
Aktuell können sich interessierte Unternehmen als »First Adopter« für die Technologien bewerben, die in der Initiative entstehen. »Unternehmen können so als erste die neuen Technologien erproben und uns mit ihrer Rückmeldung helfen, die Griff-in-die-Kiste-Software sowie sechs weitere Industrie- und Serviceroboter-Technologien zur kognitiven Robotik auf die Marktbedürfnisse und -interessen zuzuschneiden«, erklärt Kraus.
Weitere Informationen
- Deep Picking – KI-basierte Kommissionierung von Objekten
- Projektwebsite Deep Picking
- Produktblatt Greifplanung
Ihr Ansprechpartner
Werner Kraus
Forschungsbereichsleiter Automatisierung und Robotik
Telefon: +49 711 970-1049