Quelle: Materialise
Flexibilität schaffen
Marcus Joppe, Geschäftsführer von Materialise in Deutschland, stand schon Anfang der 1990er Jahre vor dem ersten 3D-Drucker Europas. Mehr als 30 Jahre später besetzt der studierte Informatiker mit seiner Expertise eine Marktnische, die in Zeiten der Digitalisierung erst so richtig an Fahrt aufnimmt.
Additive Fertigung und Industrie 4.0 sind wie füreinander geschaffen. Sie ergänzen sich wunderbar. Digitalisierung ist dabei der Schlüssel. »Die Additive Fertigung ist bereits eine digitale Fertigungstechnologie und ermöglicht schon jetzt viele der angestrebten Vorteile von Industrie 4.0«, weiß Marcus Joppe und fährt fort: »Mit ihr ist eine flexible Fertigung möglich: on-demand, dezentral und vernetzt. Zusätzlich sind die Fertigungskosten relativ unabhängig von der Bauteilkomplexität.«
Der gebürtige Bremer und leidenschaftliche Fußballfan weiß, wovon er spricht. Schließlich ist er ein Pionier auf dem Gebiet des 3D-Drucks. Bereits während seines Studiums an der Universität in Bremen unternahm er im angeschlossenen produktionstechnischen Forschungsinstitut BIBA softwareseitig erste Gehversuche, konnte hautnah den ersten 3D-Drucker Europas live und in Farbe im Einsatz bewundern. Aus der Theorie wurde schnell Praxis. Joppe arbeitete fünf Jahre als wissenschaftlicher Mitarbeiter am BIBA, bevor er sich mit einem eigenen Spin-off im Jahr 2001 ausgründete und auf Softwareentwicklung für industriellen Metall-3D-Druck spezialisierte. Das blieb im Markt nicht unbemerkt. Und so kam es, dass sein Unternehmen 2011 mit Materialise fusionierte.
Seitdem ist viel passiert. »Die erste Stufe war das Rapid Prototyping, also der klassische Form- und Musterbau von Werkzeugen und Funktionsmustern in der Produktentwicklung. Nachdem sich die Technologie konsequent weiterentwickelt hatte, ging es dann in der zweiten Stufe mehr und mehr in die Serienfertigung. Noch nicht auf breiter Front, aber für bestimmte Einsatzgebiete wie zu Beispiel die Hörgeräteindustrie. Im nächsten Entwicklungsschritt werden Themen wie Künstliche Intelligenz, Data Mining und Machine Learning eine wesentliche Rolle spielen«, ist Joppe überzeugt. Bereits vor einigen Jahren hat Materialise die Entwicklung seiner Produkte in Richtung Cloud-Native-Lösungen aufgenommen. Das erste Ergebnis dieser Arbeit kommt dieses Jahr auf den Markt und wird dem Bedürfnis der 3D-Druckanwender entgegenkommen, den Druckprozess mit Sicht auf die eigenen Anforderungen zu optimieren.
Profil
Name: Materialise
Profil: Neue Anwendungsbereiche für das hochinnovative Potenzial des 3D-Drucks zu erschließen, ist das Ziel des 1990 gegründeten Unternehmens. Zum Produktportfolio zählen Konstruktions- und 3D-Druckdienstleistungen in verschiedensten Materialien sowie Softwarelösungen. Mit seiner Softwareentwicklung verfolgt Materialise das Konzept eines offenen Ökosystems, das Anwendern, anderen Softwareunternehmen und den Maschinenherstellern durchgängige Lösungen für die additiven Arbeitsprozesse ermöglicht.
Sitz: Bremen und München als Standorte in Deutschland, Hauptsitz Belgien
Dezentrale Fertigung als Vorteil
Jüngst hat die Corona-Pandemie dazu beigetragen, die Additive Fertigung zu befeuern. Als im Frühjahr 2020 so manche Lieferkette unter dem Druck der sich veränderten Rahmenbedingungen zusammenbrach, konnte der 3D-Druck mit Flexibilität und Geschwindigkeit punkten. So wurden Masken, Schutzausrüstungen, Teile für Beatmungsgeräte und andere medizinische Produkte lokal produziert und waren in diesen volatilen Zeiten weniger von den Opportunitäten der Weltwirtschaft abhängig.
Marcus Joppe weiß: »Die frühe Vision, dass 3D-Drucker im Keller oder der Garage stehen, also jeder sein eigener Produzent ist, hat sich nicht bewahrheitet.« Und legt nach: »Dagegen erwarten wir, das 3D-Druck eine prägendere Rolle in der Produktionslandschaft spielen wird. Zukünftig wird es immer mehr Anwendungen geben, wo es sich wirtschaftlich rechnet, additiv zu fertigen. Dabei entscheidend ist und bleibt aktuell allerdings noch die Stückzahl beziehungsweise Losgröße.« Bei der Qualität, so Joppe, ständen die additiv gefertigten Fabrikate den konventionell hergestellten oft in nichts mehr nach.
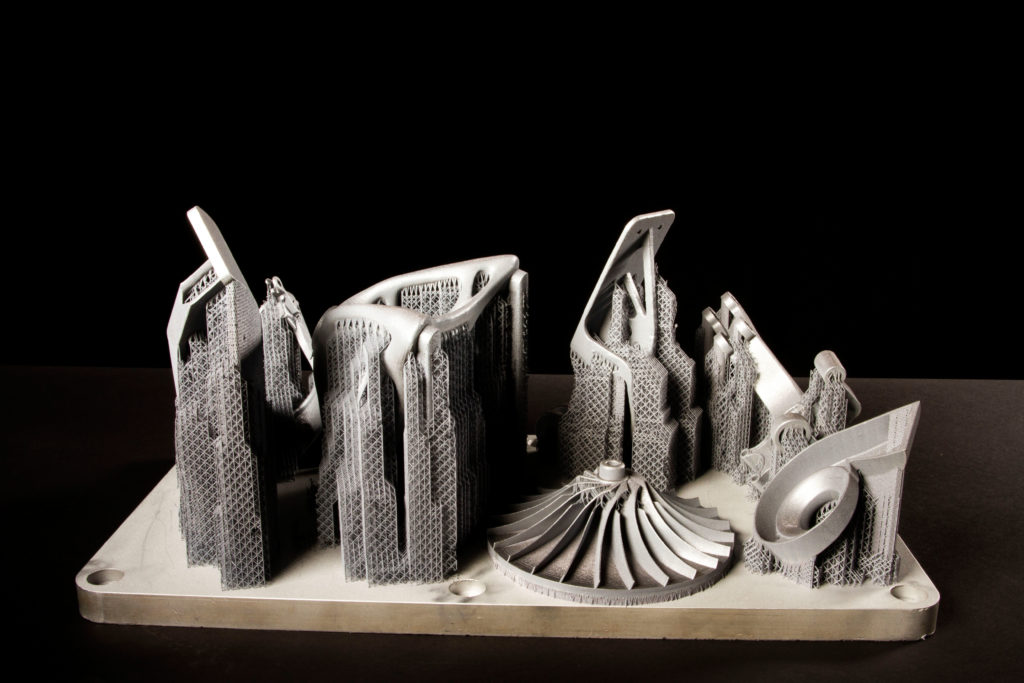
Aufseiten der Unternehmen als Nutzer der Additiven Fertigung mangelt es teilweise noch an Verständnis. Grundlegendes Wissen ist vorhanden, etablierte Anwendungen wurden projektweise bereits erfolgreich umgesetzt. Oft fehlt jedoch eine Strategie, um die sinnvolle und nachhaltige Implementierung der Additiven Fertigung in die eigenen Prozesse umzusetzen. Das war auch der Grund, warum Materialise sich an der zweiten Lernreise Industrie 4.0 als Partner beteiligte. Neben der technologischen Entwicklung sind inhaltliche Arbeit und starke Netzwerke entscheidend, um die industrielle Entwicklung durch Wissenstransfer voranzubringen. Auch die Zusammenarbeit mit Forschungspartnern wie Fraunhofer helfe dabei, die eigene Expertise kontinuierlich zu erweitern.
Weitere Texte über die zweite Lernreise Industrie 4.0 live
Drei Unternehmensvertreter berichten von ihren Erfahrungen mit der zweiten Lernreise Industrie 4.0 live und den Herausforderungen, vor denen sie aktuell stehen:
- German Edge Cloud: Effizienz in Echtzeit
- Materialise: Flexibilität schaffen
- Murrelektronik: Schon vor Industrie 4.0 digital
Fünf Anwender, Best-Practice-Partner und Mitglieder der Lernreise Industrie 4.0 live berichten von ihrem Umgang mit Tradition und Ver änderung: »Anwendungsdaten ab Werk in die Cloud flüstern«
Stefan Aßmann und Thomas Bauernhansl, die beiden Schirmherrren der Lernreise Industrie 4.0 live, im Interview: »Nach der Orientierung kommt die Fokussierung«
Peter Kreuz, Unternehmer, Bestsellerautor und Gründer von »Rebels at Work«, ruft dazu auf alten Erfolgen zu misstrauen: Gesunde Paranoia