Das Eisenwerk Bassum hat innerhalb von drei Jahren die Kapazität verdreifacht. (Quelle: EWB/Timo Lutz Industriefotografie)
So gelingt die Verdreifachung der Produktion beim Eisenwerk Bassum
Von der Manufaktur zur Serienfertigung: Das Eisenwerk Bassum stellt spezielle Behälter (sogenannte endlagergängige Container) her, die für den Rückbau von Atomkraftwerken benötigt werden. Weil die Nachfrage steigt, baut das Unternehmen seine Produktionskapazität derzeit massiv aus. Das Fraunhofer IPA hilft bei der Planung und Umsetzung.
Veröffentlicht am 22.05.2025
Lesezeit ca. 11 Minuten
Um der steigenden Nachfrage begegnen zu können, hat das Eisenwerk Bassum (EWB) in den vergangenen drei Jahren seine Produktionskapazität um etwa die dreifache Jahresstückzahl erhöht. Dafür hat EWB ein benachbartes Unternehmen aufgekauft, dessen Produktionshallen übernommen und neu eingerichtet.
Bei der Planung hat sich EWB von Roman Ungern-Sternberg, Leiter des Geschäftsbereichs End-to-End Operations am Fraunhofer IPA, helfen lassen. Um zu ermitteln, wie die Hallen für einen reibungslosen Betrieb am besten eingerichtet werden sollten, führten Ungern-Sternberg und sein Team zunächst eine Wertstromanalyse durch. Danach begann die eigentliche Fabrikplanung. Herausgekommen ist dabei ein wandlungsfähiges Produktionskonzept zur Outputmaximierung.
Nun lassen der bisherige EWB-Geschäftsführer Hartmut Grunau und Prokurist Holger Rüchel das gemeinsame Projekt im Gespräch mit Ungern-Sternberg Revue passieren.
Herr Grunau, Herr Rüchel, der Rückbau in Deutschland ist in vollem Gange und dazu braucht es zahlreiche Verpackungen. Wie wirkt sich das auf die Produktion im Eisenwerk Bassum aus?
Hartmut Grunau: Angesichts der hohen Nachfrage nach unseren endlagergängigen Stahlblechcontainern haben wir vor drei Jahren auf Wunsch unseres Gesellschafters ein umfangreiches Investitionsprogramm zum Ausbau der Produktionskapazität auf die circa dreifache Jahresstückzahl gestartet. So können wir jederzeit genug Container für den Rückbau der Kraftwerke liefern.
Zur Person
Hartmut Grunau war über 30 Jahre geschäftsführender Gesellschafter im Eisenwerk Bassum. Er hat über Jahrzehnte die Entwicklung, Zertifizierung und Produktion von Konradcontainern vorangetrieben.
Das klingt sehr ambitioniert. Wie gut konnte der Plan eingehalten werden?
Grunau: Technisch haben wir unsere Ausbauziele bereits heute erreicht. Was nicht nur unser Team, sondern auch unsere Kunden und Gesellschafter sehr freut. Die letzten drei Jahre waren sehr intensiv und wir haben unter Volllast produziert und uns verändert. Das ging nur dank der herausragenden Motivation unserer Mitarbeiter!
Verdreifachung stellt alle Prozesse in Frage, nicht nur die Produktionsprozesse
Wo genau hat sich etwas verändert und wie sind Sie die Analyse der Ist-Situation angegangen?
Holger Rüchel: Dies betraf alle Fertigungsbereiche, die Logistik wie auch die Planung. Durch die Einführung eines neuen ERP-Systems konnte diese signifikant verbessert und verschlankt werden. Basierend auf den etablierten Fertigungs- und Prüfprozessen haben wir mit der Wertstromanalyse des Fraunhofer IPA alle Prozesse in Fluss gebracht. Bei der Umsetzung haben wir uns jeweils auf den nächsten Engpass konzentriert. Und so die Fertigung von Bereich zu Bereich unter Volllast erweitert.
Zur Person
Holger Rüchel ist Prokurist im Eisenwerk Bassum und verantwortlich für Ingenieurleistungen und die Projektabwicklung. Seit seinem Eintritt im Jahr 2009 hat er sich auf die Entwicklung und Herstellung von Behältern für radioaktive Stoffe sowie verwandte Produkte und Dienstleistungen spezialisiert.
Bei einem solchen Umbau entstehen viele Zielkonflikte. Nach welchen Zielen haben Sie den Umbau organisiert?
Rüchel: Zwei Dinge waren immer klar: Die zugesagten Liefertermine sind verbindlich einzuhalten und es durfte durch die baubedingten Maßnahmen auf dem Werksgelände zu keinem wesentlichen Produktionsausfall kommen. Das war die Kunst.
Flexibler, flussorientierter Masterplan
Wie ging es mit der Analyse und Gestaltung dann weiter?
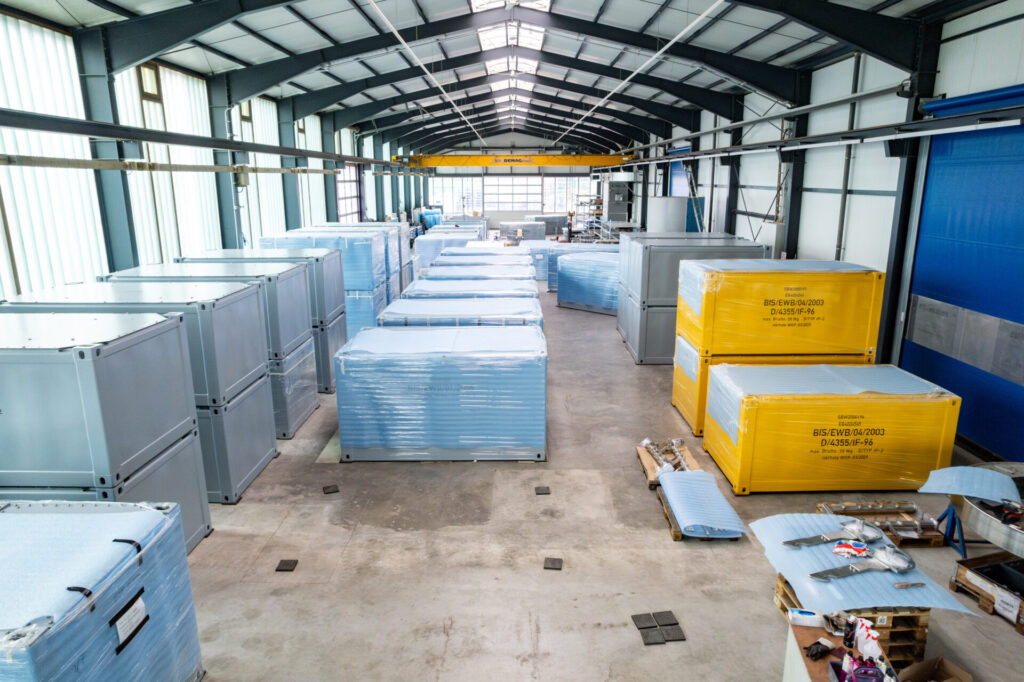
Grunau: Wir haben zunächst unsere Wertströme analysiert. Und zwar vom Stahleinkauf bis zum fertigen Container. Hierbei sind auch die vielen verschiedenen, individuellen Inneneinbauten und Abschirmvarianten der ansonsten standardisierten Außenbehälter berücksichtigt worden. So haben wir neben der Etablierung einer industriellen Serienfertigung für die Massenkomponenten die erforderliche Manufaktur zur Erfüllung der spezifischen Bedarfe der Kunden aus dem Rückbau berücksichtigen können! Wir sind Dienstleister und liefern individuelle Lösungen.
Ein solches Wachstum lässt sich nicht im Bestand realisieren. Wie haben Sie den Standort erweitert?
Grunau: Wir konnten die Produktionshallen des Nachbargrundstücks erwerben und den Standort Sulingen in die EWB integrieren. Das waren die wesentlichen Erweiterungen.
Was würden Sie jedem empfehlen, der eine solch komplexe Layoutplanung vorhat?
Grunau: Legen Sie sich nicht zu schnell auf eine Lösung fest. Wir hatten viele wirklich unterschiedliche Varianten entwickelt und haben diese umfänglich bewertet. In der Umsetzung konnte der Plan in wesentlichen Bereichen aufgrund fortschreitender Erkenntnisse noch weiter verbessert und angepasst werden. Eine solche gewisse Flexibilität ist sicherlich hilfreich.
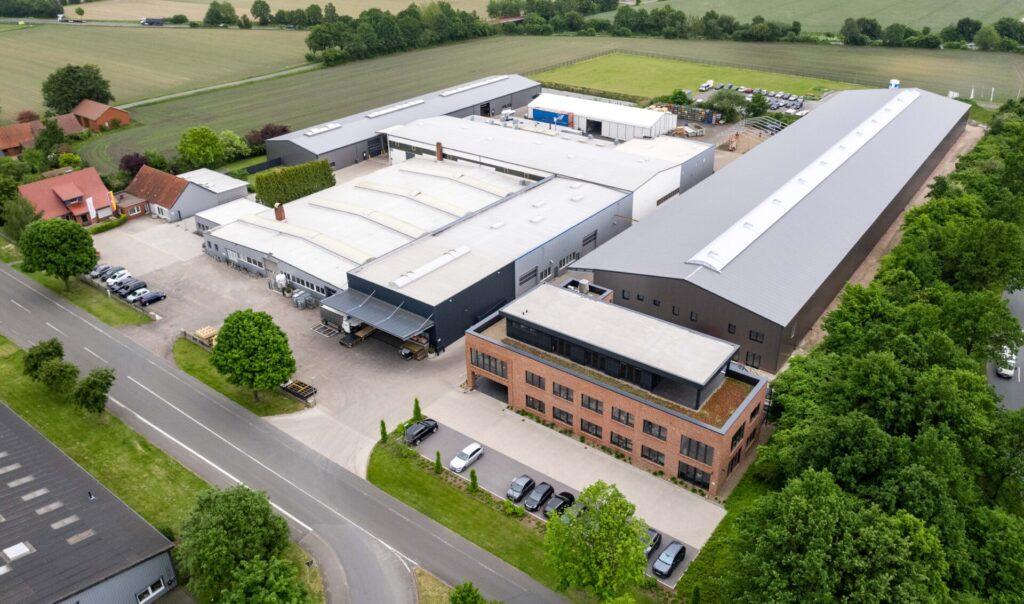
Haben Sie dafür ein Beispiel?
Grunau: Unser Betonierbereich wurde gegenüber dem ursprünglichen Konzept mehrfach konzeptionell überarbeitet, bis wir technologisch und ökonomisch zufrieden waren. Unsere doppelwandigen Container wiegen bis zu 16 Tonnen. Da spielt eine schlanke Logistik und der Materialtransport auf dem Werksgelände eine große Rolle. Am Ende haben wir einen Routenzug etabliert für unsere Container. Das ist sicherer und einfacher als der Transport per Stapler.
Robuste Automatisierung schafft Freiräume
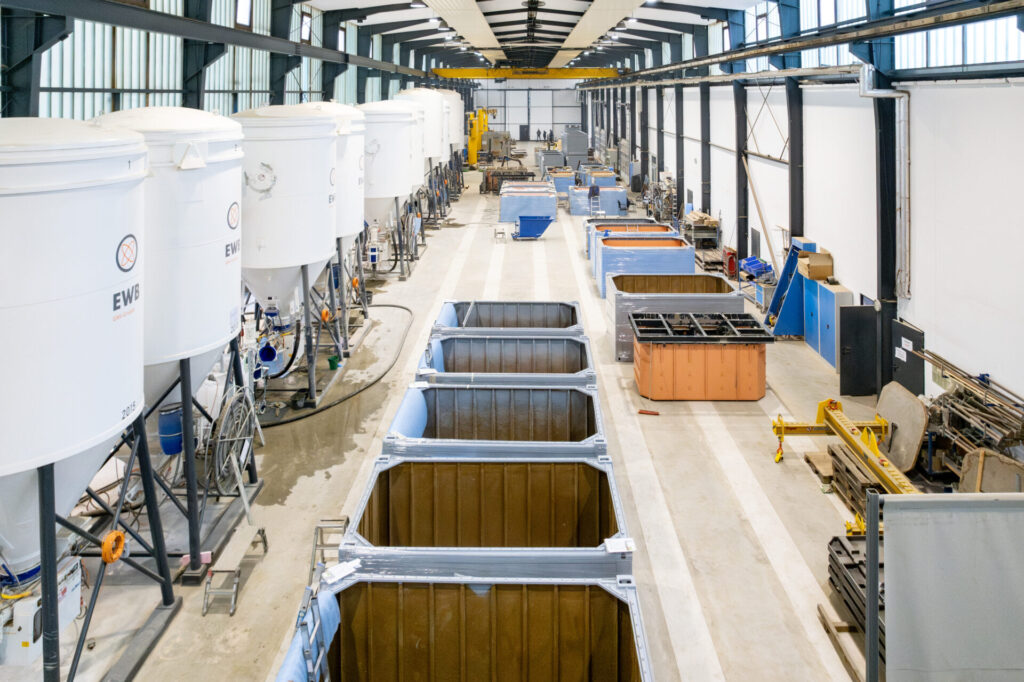
Gerade bei der aktuellen Fachkräftesituation ist Automatisierung immer ein Thema. Nach welchem Prinzip haben Sie Prozesse automatisiert?
Rüchel: Produktqualität und die Ergonomie für unsere Mitarbeitenden sind das A und O. Die automatisierte Schweißtechnik ist so weit, dass Nähte selbst bei komplizierten Geometrien vollautomatisch geschweißt werden können. So haben unsere Schweißfachkräfte mehr Zeit für die präzise Vormontage und Qualitätsprüfung.
Welche Prozesse standen ganz oben auf der Automatisierungsliste?
Rüchel: Neben den Schweißprozessen vor allem der Laserzuschnitt mit automatisiertem Blechlager und die Strahlentrostung vor der Beschichtung. Hier fertigen wir nahezu vollautomatisch.
Bedeutet eine hohe Automatisierung nicht eine neue Abhängigkeit? Stichwort: komplexe Robotertechnik.
Rüchel: Unsere Kernprozesse sind redundant ausgelegt. So können wir die einzelne Anlage am optimalen Betriebspunkt betreiben. Und sind bei Störungen weniger anfällig. Zudem haben wir die Möglichkeit, Verbesserungen im direkten Vergleich zu sehen.
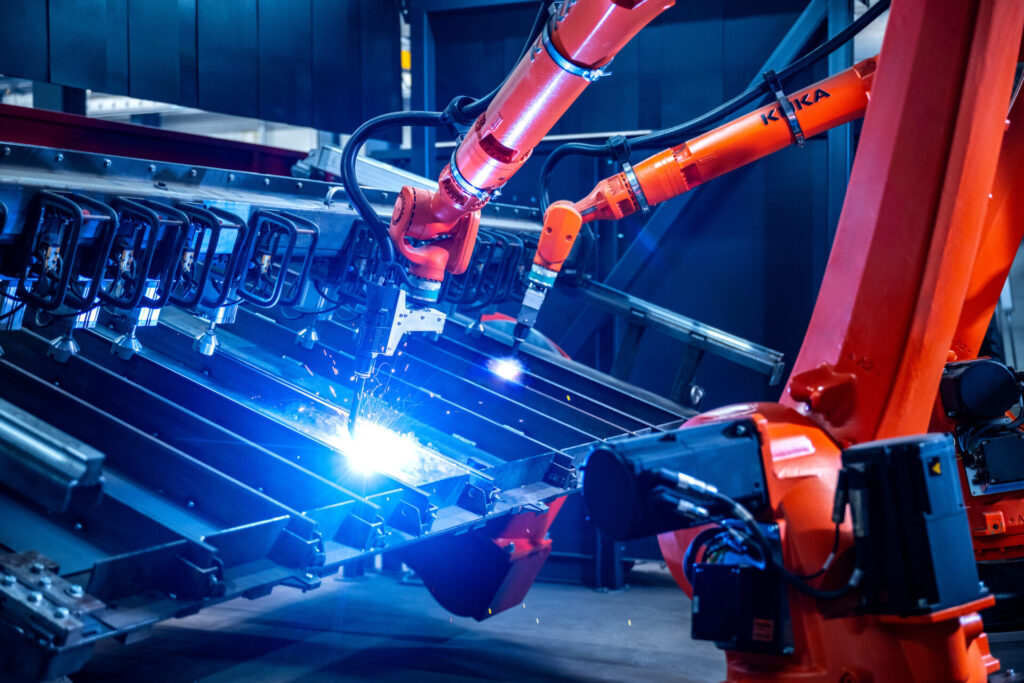
Vollautomatisierung und personenlose Schichten sind in aller Munde. Welche Philosophie verfolgen Sie?
Rüchel: Wir haben gute Erfahrung gemacht mit dem Prinzip »90 Prozent Automatisierung« in einem Prozess. Die letzten zehn Prozent sind manuell. Beispiel ist das Sandstrahlen mit der neuen Durchlaufstrahlanlage. Die Qualitätskontrolle und das Finish bleiben manuell. Damit entlasten wir einerseits unsere Mitarbeitenden stark. Andererseits bleibt die Komplexität der Anlagen für einen mittelständischen Betrieb handhabbar.
Ohne ERP geht es nicht
Heutzutage geht’s bei Automatisierung ja nicht nur um die direkte Wertschöpfung. Auch die Planung und Steuerung der Produktion wird automatisierter.
Grunau: Stimmt genau. In der Manufaktur kennt jeder Mitarbeitende noch jeden Containerauftrag persönlich. Das geht mit unseren neuen Stückzahlen schlicht nicht mehr. Wir haben also zum Kapazitätsausbau noch ein neues ERP-System eingeführt.
Bei ERP-Einführungen hört man oft von viel Frust. Was würden Sie beim nächsten Mal wieder genauso machen und was definitiv nicht mehr?
Grunau: Für die Implementierung wurde mehr Zeit und Schulung benötigt als geplant. Aber von Frust kann keine Rede sein, denn die Alternative – ohne ERP – wäre nicht beherrschbar gewesen. Das war uns allen klar. Hilfreich war für uns die methodische Begleitung des Fraunhofer IPA aus Produktionssicht. Die richtige Anpassung des ERP ist das Eine, die logistisch optimale Abbildung der Wertströme im ERP etwas ganz anders. Also welche Teile disponieren wir wie, wo ergeben Lagerstufen Sinn und wie passt das alles zum Wertstrom.
Die Vielzahl an strukturierten Daten umfänglich zu erfassen ist allerdings keine einfache Aufgabe und das bedarf einer sehr engen Begleitung. Ist die Datenqualität erst erreicht, begeistert das ungemein. Dann laufen viele Prozesse plötzlich automatisch, die vorher sehr viel manuelle Arbeit gemacht haben. Zum Beispiel die vollständige Termin- und Materialplanung.
Ein wichtiger Punkt bei der Digitalisierung ist auch die digitale Prozessdokumentation. Wie haben Sie den Übergang von der analogen zur digitalen Dokumentation geschafft?
Grunau: Dieser Prozess ist noch nicht abgeschlossen, aber für uns eminent wichtig, denn ohne die Fertigungsdokumentation ist die Hardware in einer sicherheitstechnisch sehr anspruchsvollen Branche nichts wert. Die digitale Dokumentation wurde mit dem ERP-Projekt verknüpft geplant und wird nun im Detail sukzessive ausgerollt. Hier geht Gründlichkeit vor Schnelligkeit.
Tipps für die Umsetzung im Projektmanagement
Wie haben Sie das Projekt »Outputmaximierung« strukturiert?
Rüchel: Zunächst mit der Frage: In welchen Stufen kann der Ausbau genau erfolgen und in welcher Menge kann damit verbunden die Stückzahl im Sinne eines Stufenplans gesteigert werden? Welche Maßnahmen und Investitionen sind damit verbunden?
Der Stufenplan beinhaltet dann alle Einzelaktivitäten?
Rüchel: In jeder Stufe haben wir die kritischen Arbeitspakete zusammengefasst, die eine neue Lieferleistung gegenüber dem Kunden ermöglichen. Pro Stufe standen dann ein paar zentrale Engpässe, wie Maschinen mit ihren Lieferterminen, im Fokus. Die kontinuierliche Verbesserung lief natürlich parallel weiter. Sich verbessern ist ja nicht an einen Termin gebunden, sondern geht jeden Tag.
Für so einen Umbau braucht man ein starkes Team. Welche Tipps würden Sie einem Produktionsleiter oder Geschäftsführer geben?
Rüchel: Absolut, ein Produktionsleiter lebt von seinem Team, also von seinen Meistern und von den Erfahrungsträgern in der Fertigung. Hier ein schönes Beispiel zur Kreativität unseres Teams: Wir haben die Rüstzeiten auf den neuen Anlagen radikal reduziert und sind so deutlich flexibler. Der Vorrichtungsbau war dabei eine wirkliche Teamleistung aus AV, Meistern und allen Mitarbeitern vor Ort. Eine geschlossene Teamleistung und die Rückendeckung durch die Unternehmensleitung sind wichtig in anstrengenden Zeiten.
Grunau: Uns hat der regelmäßige Blick von außen sehr geholfen. Und zwar nicht im Sinne von Ausführungskontrolle, sondern als Sparring und für die gemeinsame Diskussion. Ansonsten vergisst man im Tagesgeschäft schnell etwas. Gemeinsam mit dem Fraunhofer IPA haben wir uns als Führungsteam mehrmals pro Jahr getroffen und die kritischen Punkte diskutiert und unsere Konzepte angepasst.
Wie geht es nun weiter?
Grunau: Wir haben nun die Aufgabe, die sehr stark in kurzer Zeit gewachsene Organisation mit der neuen Führungsstruktur auf diesem Niveau fest zu etablieren und Abläufe im Detail zu optimieren. Interne Schulung, Digitalisierung und Vertiefung unserer Kompetenzen sind hier sehr wichtige Themen.
Herr Grunau, Herr Rüchel, vielen Dank für die Einblicke in die Produktion!
Ihr Ansprechpartner
Roman Ungern-Sternberg
Geschäftsbereichsleiter End-to-End Operations
Telefon: +49 711 970-1976